Value of the ConX® System
Stakeholder Advantages
Benefits of the ConX Steel Framing System
- 2x-5x faster than conventional steel
- 10,000 -15,000 sqft. assembled/day
- We will give you a minimum of a month back in schedule
- Expedited occupancy for client
- Faster design through delivery than any other structural alternative
- Rapid turn over to other follow-along trades
- Standard processes expedite cycle time
- Pre-fabricated components accelerate delivery schedule
- Pre-approved connections accelerated plan checks and regulatory approvals
- One of the safest steel erection systems available
- Fewer “at-risk” hours on site due to minimal field personnel and accelerated schedule
- “Lower and locking” connections provide instant stability and alignment to structure prior to bolt up
- All erection is done from aerial lifts and baskets and tied-off-at-all times
- Minimal to no field hot work
- Precision fabrication and connections translate to repeatable standardized work
- High quality and tolerance yield perfect fit in the field
- 50% reduction on field labor for assembly
- Less on-site disruption
- We have NEVER missed a schedule… EVER
- 15+Million sqft delivered and growing
- Superior building performance with efficient design at a competitive cost
- Patented technology
- Progressive collapse and blast resistance of the ConX System meets the most stringent building code criteria including: ATFP (Anti-Terrorism Force Protection), UFC (Unified Facilities Criteria), AISC codified, permitted by California’s Office of Statewide Healthcare Planning and Development (OSHPD), Division of State Architect (DSA) and other regulatory agency requirements.
- Rigorously tested in full scale environment, ConXtech has undergone 17 full-scale tests at the University of Arizona’s Structural Lab in Tucson, and 60+ full scale destructive tests.
- Standard detailed kit of parts simplifies the project life-cycle from design through erection
- Standard connections used redundantly simplifies interface with other systems and finishes
- Entire team can organize around digital chassis with high value digital Building Information Modeling (BIM) at earliest stages of design
- Patented technology inherently simple and repeatable
- Lean inspired to eliminate process and product waste
- Structural simplicity no more no less
- Cost certainty: As a modular system we will give you a definitive price (+/- escalation)
- Schedule certainty: We have never missed a schedule… EVER
- Quality certainty: Every piece fabricated is tracked and measured through our robust automated quality analysis system
- Systematized approach yields predictability of building performance
- Each building is designed by our in-house professional engineering team with over 50 years collective of experience.
- Fit up certainty
- You can be certain our dedicated team will give you 100%
- Speed to market: Earlier occupancy revenue
- Early preferred returns to investors
- Up to 10% lower all in cost when compared to conventional steel (Including savings in GC/CR’s)
- Reduced carrying cost and interest reserves
- Easily integrated with other trades due to standard modular componentry
- Accelerated approvals
- Lower overall risk with greater predictability due to systems approach
- Reduction in labor cost
- Reduction in safety risk
- Offsite pre-fabricated work decreases need for onsite labor
Building to a Higher Standard™
- 2x-5x faster than conventional steel
- 10,000 -15,000 sqft. assembled/day
- We will give you a minimum of a month back in schedule
- Expedited occupancy for client
- Faster design through delivery than any other structural alternative
- Rapid turn over to other follow-along trades
- Standard processes expedite cycle time
- Pre-fabricated components accelerate delivery schedule
- Pre-approved connections accelerated plan checks and regulatory approvals
- Reduction of peak capital investment due to schedule acceleration
- Reduced carrying cost and interest revenues required for development financing
- Lower total install cost than conventional structural steel solutions by up to 10%
- One of the safest erection systems ever
- ConX brings reductions in wrap-up rates and insurance costs for owners/developers. A safe environment, a shorter construction schedule and high-quality structure generates a favorable risk profile for assembly, workers comp, course of construction, builder’s risk, and construction defects
- ConX dramatically improves on wood frame building solutions by drastically reducing mold, rot, and shrinkage concerns. ConX is non-combustible and provides a more sound and sturdy structure built to resist earthquakes, wind and other elements. The insurance industry has been quick to recognize many of the advantages ConX brings, and we are pleased that selected insurance providers now offer substantially lower wrap-up and other insurance premiums on projects which utilize the ConX System
- The ConX System enables a spatially and dimensionally accurate ConX Digital Chassis to be established at the earliest concept stage. All stakeholders then leverage the chassis as the collaborative platform for efficient integration. The result is fewer iterations and a more predictable cost-efficient project delivery.
- The ConX System is so precise that definitive pricing of the structural component of a budget can be determined early in the design process. This precision, along with cost savings the system brings to overall efficiency, can make the difference between making a project “pencil” or not.
- Whether it’s a mission critical data center, medical office building, hospital, education, commercial, or another structure, owners/developers demand high quality at a reasonable cost. The ConX System provides a premium structure at a cost competitive price, while reducing the long-term maintenance liability.
- The precise and elegant simplicity of the ConX System means perfect fit up in the field. Before field construction begins, custom components for your project are pre-fabricated in a high-tech manufacturing facility. The cutting, drilling, milling, and welding of components and assemblies for your project are pre-built to tolerances as close as six one thousandths of an inch. Each piece is qualified through our robust automated quality process.
- When it’s time for field assembly, the ConX interlocking collar technology allows the beams to “lower and lock” onto columns where they are bolted. Welding on-site is minimal, reducing the need for on-site labor which leads to lower construction and overhead costs, a reduction of safety risks to workers, and lower costs for special inspections.
- Steel is the most recycled content in the world the only true “cradle-to-cradle” recycled material
- With completely reusable components by design, our structure can be completely repurposed
- ConXtech Collar forgings are 100% recycled material and ConXtech steel 97% recycled
- 5-30% structural steel weight reduction translates to reduces CO2 emissions
- Schedule acceleration yields 5%+ energy reduction
- Offsite pre-fabrication equates 20% reduction of waste by reducing onsite labor
Rapid, Organized and Predictable Workflow
- We are 70% faster than conventional steel and concrete
- 10,000-15,000 sqft. assembled per day
- We will save you a minimum of 1 month in schedule, what is that worth to you?
- If you want a steel structure that is 40,000+ sqft., 2-10 stories in height, and you want it fast, ConXtech offers a cost competitive solution for any market sector in any geographical region.
- Expedited approvals processes
- Vastly reduced lead times due to a finite set of ConX components, design simplicity and steel members which are readily available
- Vertical construction of a full-height building frame expedites other follow-along trades. MEP and other trades can start within days of the commencement of construction, often concurrently, optimizing crews.
- ConX is one of the safest structural steel building systems available
- Reduced “at-risk” hours
- ConXtech has NEVER missed a schedule…EVER!
- ConXtech can lower the risk for Design Build, EPC and other Contractors. ConX is simply faster, simply safer and a simply proven Flexible Modular Structural Steel Building Solution when compared with conventional steel or other structures
- Innovative steel connection design, technology and automated processes from concept through delivery, all contribute toward unprecedented quality, efficiency and structural performance of ConX buildings
- ConXtech can lower the risk for Design Build, EPC and other Contractors. ConX is simply faster, simply safer and a simply proven Flexible Modular Structural Steel Building Solution when compared with conventional steel or other structures
- A greener solution than any conventional alternative. Lighter structure, efficiently built, lower CO2 emissions overall, vastly reduced manpower in the field.
- Reduced site disruptions
- ConXtech will save you 10% on all in total install cost compared to conventional steel
- Reduced labor cost due to schedule acceleration and lower numbers of field personnel needed
- Reduced carrying costs and interest reserves required for development financing
- Our professional engineering team will create the optimal building solution as early as a concept exists
- We will provide you with definitive price certainly(+/- escalation) at no cost
- Our team integrates and collaborates early offering a turnkey approach from design through to erection. Unlike some of our competitors, we are offer a one-stop shop for project management from preconstruction to project completion
Exercise Your Full Creative Capacity
- ConX offers a revolutionary integrated structural system without compromising architectural style. Highly configurable and flexible, the ConX System is able to accommodate variable-bay spacing and floor heights. Architects can now maximize exterior openings, infinitely configure interior spaces, and create multi-story interior volumes with unprecedented freedom.
- Our steel frame components can be easily adapted to accommodate a majority of architectural concepts both structurally and aesthetically. If project requirements are known and communicated to ConXtech early in the conceptual design process, our integration team can assist in optimizing your project structurally as well as aesthetically. The architect determines the aesthetic and functional requirements and then designates the required beam length (bay spacing) and foor-to-foor height.
- The key is to start early in the design process and assess whether ConXR™ or ConXL™ offers tangible advantages over other structural options. ConX is not limited to square or rectangular structures. Regardless of your specific project requirements, the ConXtech concept remains the same; we use technology such as BIM, CAD, CNC machine centers and robotics to design and manufacture a finite set of precise components and assemblies; columns, beams and connections which can be configured to build your structure.
- ConXtech’s goal is to vastly simplify building – without limiting the design team aesthetically. Most building footprints can be accommodated and engineered utilizing ConXFrame – including radiuses, angles, and highly articulated buildings.
- ConXtech designs using a hybrid approach – a mix of conventional structural elements integrated with ConXFrame components to aid in rapid erection. A hybrid ConX structure with a few conventional structural elements such as Braced Frames will, in most cases, still be less costly and erected much faster than a conventional steel or concrete building while delivering greater design flexibility.
- For architects in the high-density residential space are the freedom to place a ConXR structure on a flat concrete podium without the necessity to align the load path of the ConXR structure above the podium, with the concrete columns supporting the podium below. This enables completely independent layout of the residential and parking grids and the opportunity to optimize of both. In structural applications requiring longer more open bay spacing, ConXL™ is the perfect solution. This system takes the steel structure all the way down to the foundation – through parking, retail, and other uses.
Engineering With Proven Technology
- ConXtech’s professional engineers work with the SEOR to provide upfront design-assist to optimize design efficiency and generate tangible deliverables (ETABS, Revit, Standard Details, Design Calculations and Criteria)
- ConXtech can also act as SEOR in design/build pursuit
- Our in-house structural engineers have decades of experience optimizing building performance while creating efficiencies, reducing weight, minimize foundations and accelerating schedules
- Our professional engineers partner with owners and engineers early to accelerate the design from napkin sketch to a full BIM
- Standard “kit of parts” designed for rapid assembly
- ConXtech provides a standard set of details to accompany all designs
- Blend of patented and standard connections all designed to work together in a complete frame
- Complete selection of framing available, from gravity frames to moment frames, and brace frames work with our patented bi-axial moment frame collar connection
- The simplicity of a systems approach enables the Structural Engineer of Record (SEOR) to quickly grasp and efficiently apply the ConX technology. Engineers quickly become proficient in designing with ConX because the system utilizes a finite number of structural connections to achieve a wide range of structural configurations
- The ConX collar connections are pre-qualified as a Special Moment Frame and codified by the American Institute of Steel Construction (AISC) and published in AISC 358-16 Prequalified Connections for Special and Intermediate Steel Moment Frames for Seismic Applications for use by structural engineers worldwide. It is also approved by the Office of Statewide Health Planning and Development (OSHPD) for use in California hospital facilities and the Division of the State Architect (DSA) for use in California schools. ConX is LA city (LABDS) approved and meets special detailing requirements for the most demanding seismic loading as well as the current U.S. Department of Defense anti-terrorism standards for blast and progressive collapse resistance.
- The system has been scrupulously reviewed, tested through 90+ full-scale destructive tests, documented and proven – with over 15+ Million square feet designed/built to date.
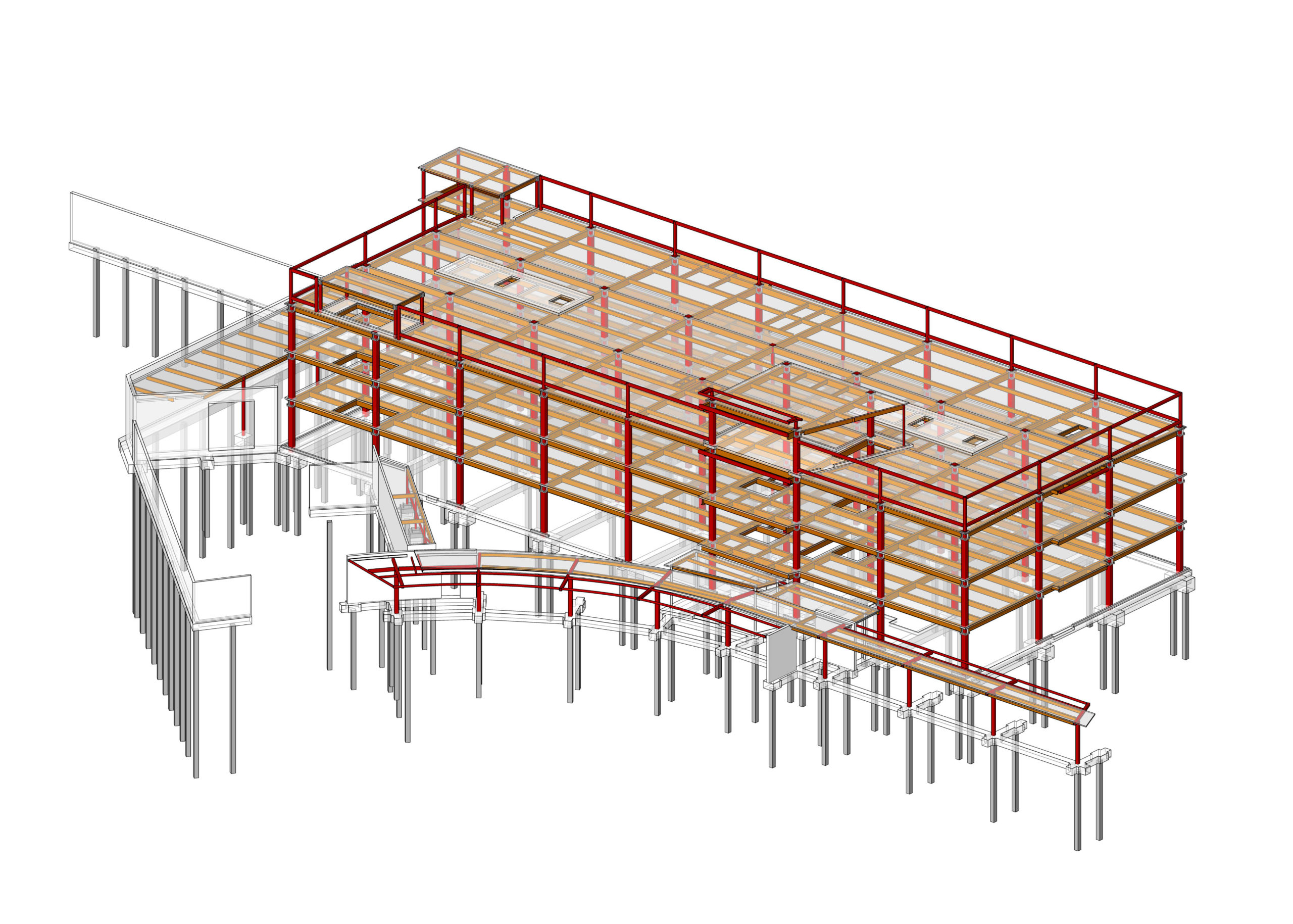