SECTION 1
A UNIQUE ACCELERATOR IN THE STRUCTURAL ENGINEER’S TOOLKIT
ConXtech: A Unique Accelerator in the Structural Engineer’s Toolkit
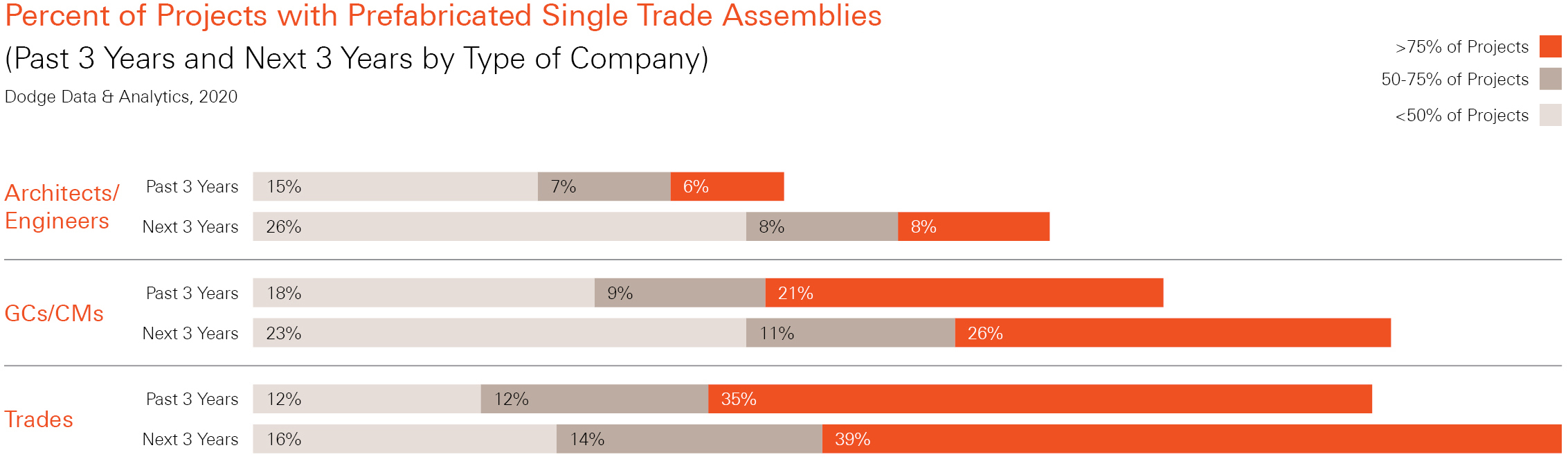
Prefabricated and modular methods of construction are not new, but their use is surging across the global construction sector. Global markets have experienced a significant uptick in demand for everything from pre-manufactured assemblies to volumetric modular apartments built offsite. Real estate developers are driving much of the sector’s growth, hoping to achieve faster construction schedules that produce earlier revenue and lower overall carrying costs. In their 2019 report, Modular construction: From projects to products, McKinsey researchers brought wide attention to the positive impacts of offsite construction manufacturing – finding that certain forms have a consistent track record of accelerating project timelines by 20% to 50%.
Offsite constructed systems range from prefabricated roof trusses to fully-finished, factory-built housing units, and the use of such systems is on the rise. In a report published by Dodge Data & Analytics, Prefabrication and Modular Construction 2020, 31% of engineers and architects, and 58% of general contractors reported that using some form of prefabrication meaningfully improved overall project timelines. Almost 70% of architects and general contractors in the Dodge study anticipated specifying single-trade prefabrication over the next 3 years.
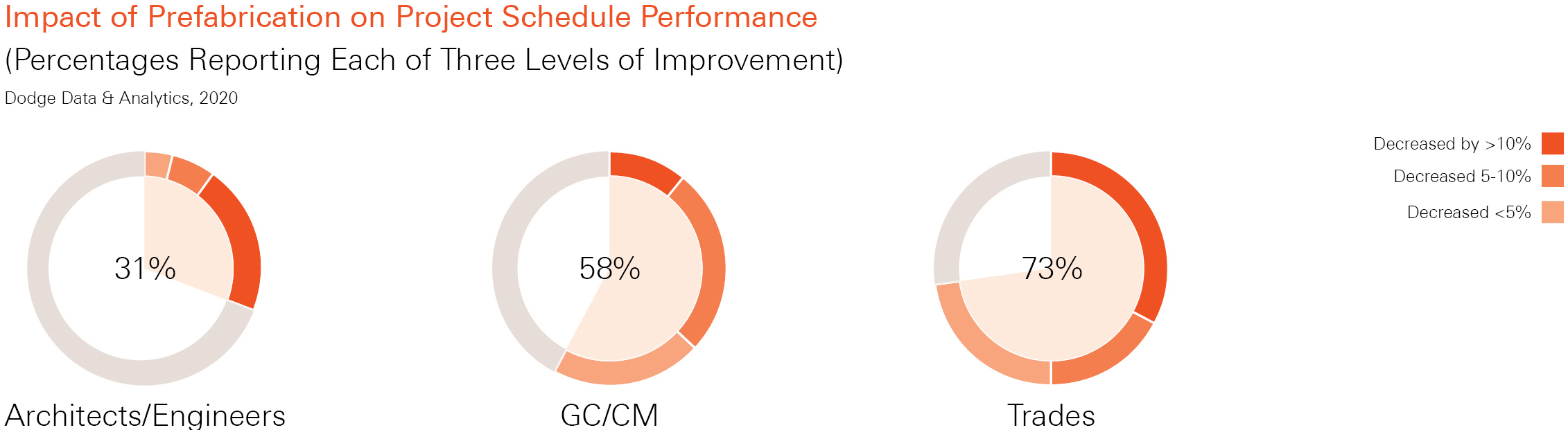
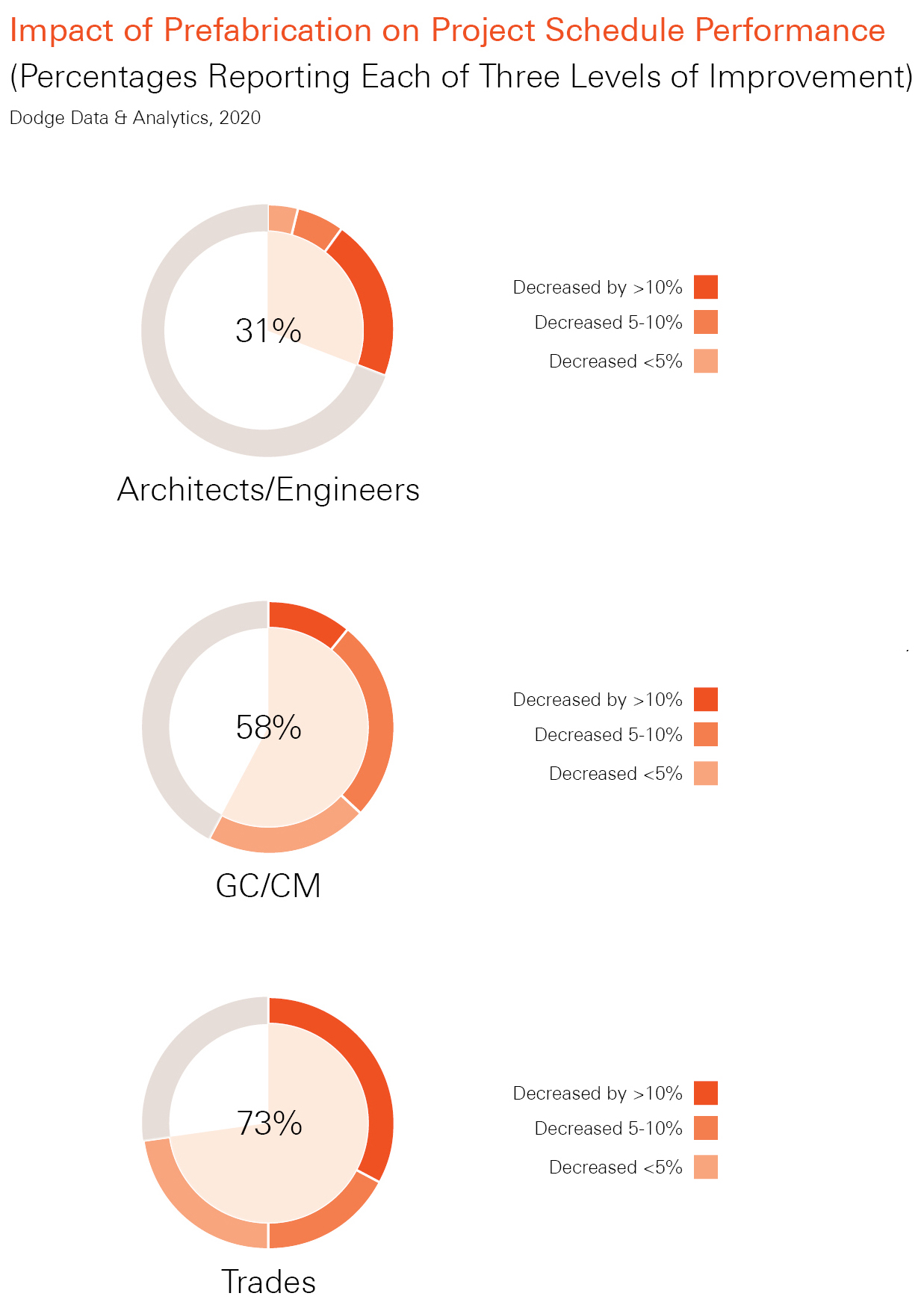
In addition to project schedule acceleration, moving complex building assemblies into a controlled factory environment promotes improved safety, sustainability, and quality metrics.
SECTION 1
PREFABRICATED STRUCTURAL SYSTEMS
ConXtech’s Prefabricated Structural Systems
Imagine a MeccanoⓇ kit or ErectorⓇ Set that’s sized for real buildings. In 2004, ConXtech founders imagined this very thing – and the result was a patented system for steel erection that has been accelerating projects and delighting general contractors ever since. ConXtech’s effectiveness and success are due to the elegance and simplicity of its system. Each steel member is engineered and precisely fabricated, and ConXtech’s patented moment collars and gravity connections are attached at the factory – making it easy for ConXtech crews to slot members easily together on-site without field welding. In many cases an entire building structure can be assembled by a crew ⅓ the size of a traditional steel erection crew.
The system is simple by design, making it easy to specify, price, and install. The kit of parts includes the company’s signature moment frame collars, plus a wider variety of connections and assembly details suitable to address a broad spectrum of building requirements.
This white paper will provide a basic understanding of the ConXtech system that will be specifically useful for engineers and architects, along with helpful tips for owners and general contractors – along with some guidelines on best project application and practices for using the system on your projects. First – a brief introduction to the spectrum of components that ConXtech has developed for rapid connection at the jobsite:
Standard Kit of Parts:
ConXtech Moment Frame Beams & Columns
There are three basic system offerings under ConXtech’s patented moment frame system, primarily to address different building types and sizes. Each system features a standard tube steel or boxed column with prefabricated collars, with a range of beam sizes (spans) available within that system type.
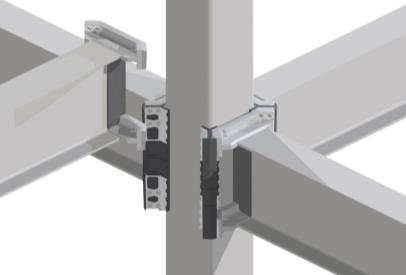
The CONXL400 is the most robust and widely used system, and is well suited for healthcare, MOB, commercial and institutional sectors. The wider bay sizes offer the most flexibility for office spaces that change over time. This system features 16” HHS or boxed columns and bay sizes can range from 18’ – 45’.
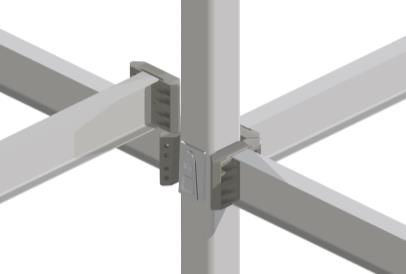
The CONXR200 is well suited for high density residential, hospitality, senior and student housing projects because of its lighter structure, and smaller column sizes. The system features 8” HHS tubed steel columns and bay sizes can range from 8’ – 24’.
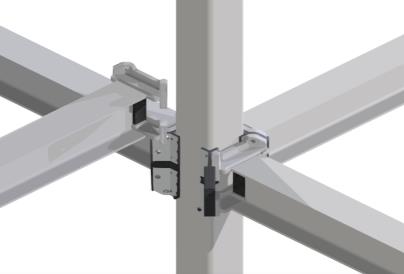
The CONXL300 is well suited for process industry pipe racks, manufacturing, and certain office environments. The system features 12” HHS or boxed columns and bay sizes can range from 12’ – 30’.
SECTION 1
CONXTECH GRAVITY CONNECTION
ConXtech Gravity Connection
The most utilized connection in the ConXtech toolkit is a gravity connector that features a laser cut bolt saddle as the lowest bolt in a vertical row of bolts. This double shear plate connection is designed for crews to assemble in the same “lower and lock” fashion and with nearly the same speed as the ConXtech moment collars.
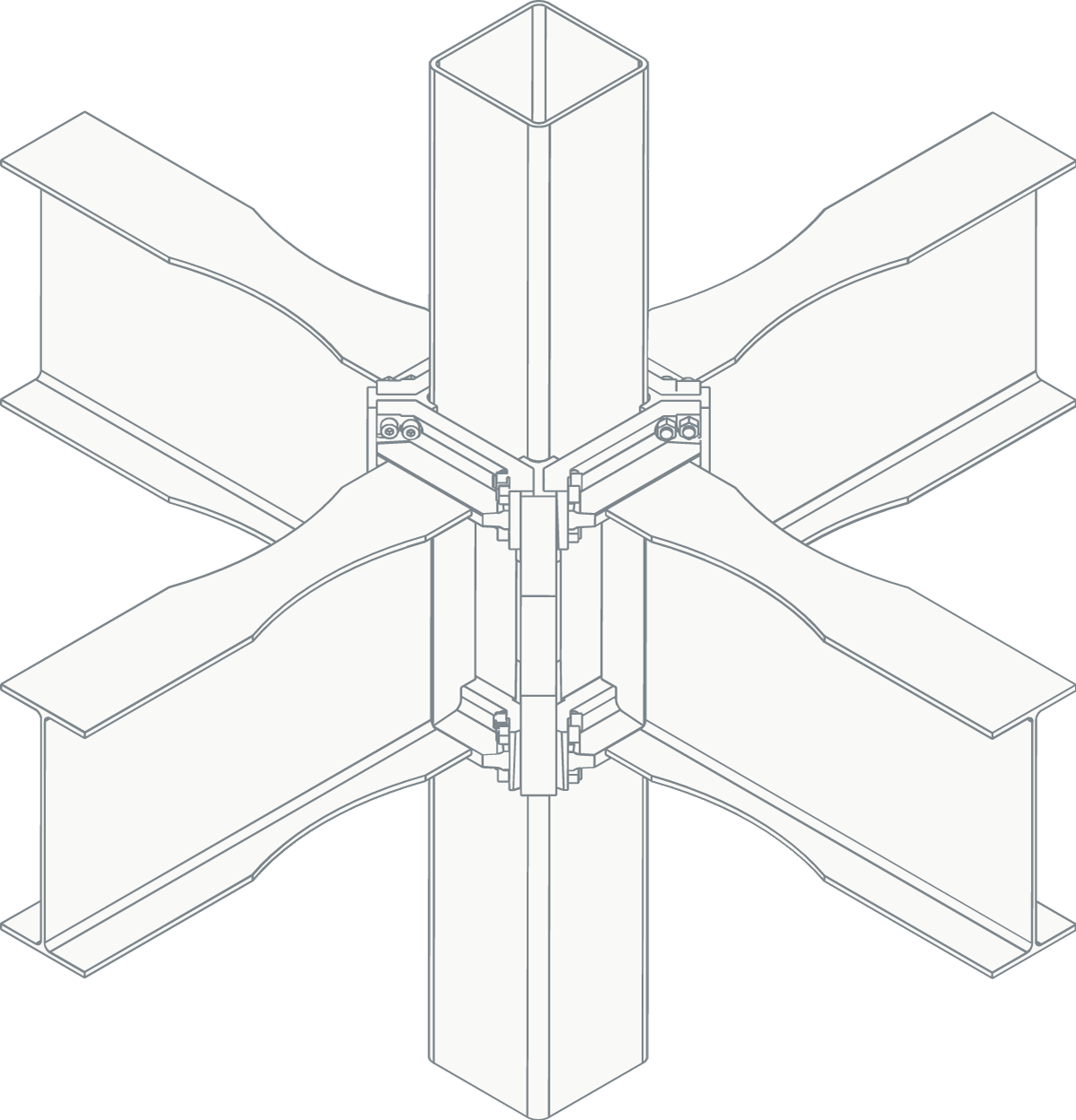
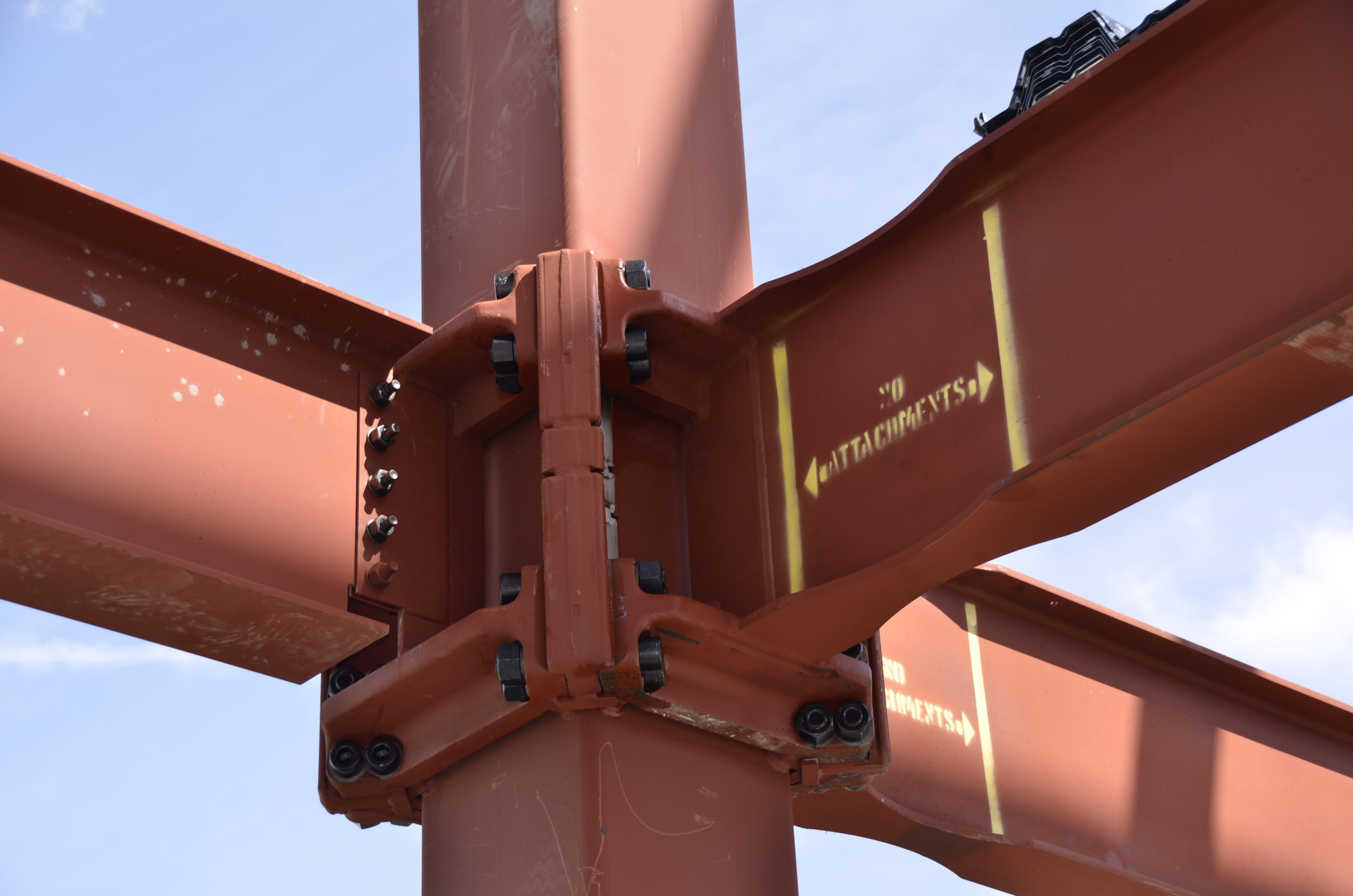
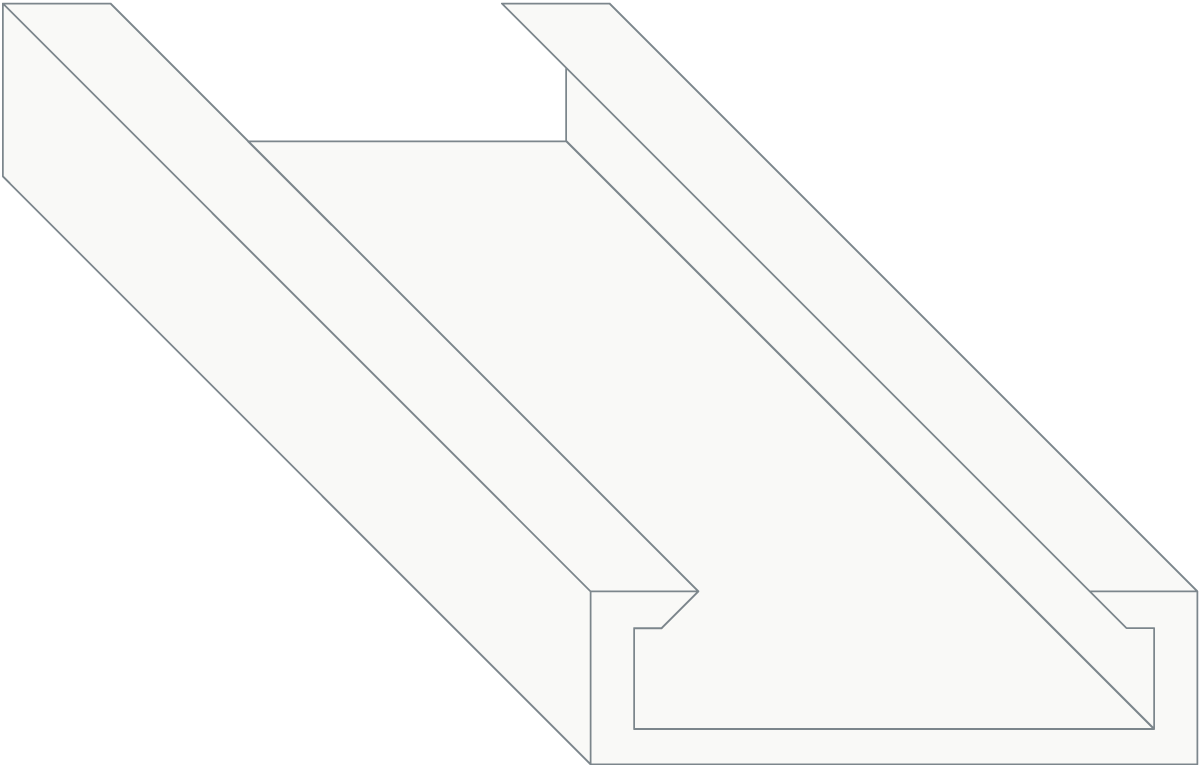
Conventional Connections and Steel Framing
While the drivers of acceleration on a ConXtech building are its special ConXtech connections, the system is entirely versatile, and ConXtech collars might be paired with more traditional steel elements such as brace frames and moment frames where more appropriate on a given project. During the Schematic Design phase, the ConXtech engineering team can help to reduce or eliminate the number of field-welded conditions to optimize for erection speed during construction.
All ConXtech steel members, connection collars and flanges are precision-manufactured to order and quality inspected in the shop environment to ensure tight tolerance and perfect fit-up in the field. The patented features of the collars and the specialty fixturing used in the shop neutralize quality issues and imperfections of rolled steel, allowing for guaranteed fit-up every time, with beam-setting speeds under 10 seconds per piece.. Crews guide the beams into position above the joint and let the specialty connector plates fit the member into a fully secured and aligned position under the influence of gravity, using hands-free Lower and LockTM technology built into the connectors. Crews are able to perform all of the main steel erection from the safety of elevated work platforms, as opposed to a traditional method, where workers are required to climb upon beams and columns to align and bolt (or weld) connections using hand tools.
The ConXtech erection method, facilitated by “lower and lock” connections, enables crews to erect a single bay to full height (8 stories or the maximum working height of the elevated work platform, whichever is less) before erecting adjacent structural bays. In the words of Bill Fisher, Senior Superintendent at MATT Construction, “ConXtech goes up and gets out of the way, so I can get my other trades in the building sooner.”
SECTION 2
SPECIFYING CONXTECH AS AN ENGINEER
Specifying ConXtech as an Engineer
ConXtech is fully prequalified as a special moment frame for high-seismic projects. It’s codified in AISC 358, AISC 341, IBC and CBC. California jurisdictions with stricter design requirements, such as DSA and OSHPD have also approved for ConXtech use on public schools and hospitals.
In 2018, ConXtech expanded its product catalog and building footprint nationwide to offer hybrid solutions for non-seismic zones.
Engineering support materials and worksheets are available (click here) through the company to assist with calculations required by the AISC 358 Chapter 10 design requirements. Unlike the other prequalified moment connections in AISC 358, the size, number, and location of the bolts, the thickness of the various weldments to the beam and column, and the sizes of all of the welds do not change as they are all sized to support the largest possible beam. The calculations produced by the designer serve to demonstrate the capacity of the load path rather than determine the size and strength of the constituent parts. The columns and beams of the Special Moment Frame must be adequately sized to control the lateral displacement of the structure and resist all of the applicable load combination forces in ASCE 7 without exceeding the available strength of the members as determined by AISC 360. The members shall also be designed and detailed in accordance with AISC 341 seismic provisions, and the ConXL400 moment connections shall meet all of the eleven design checks required by AISC 358 chapter 10.
To make the design process as efficient as possible, ConXtech provides engineers with a standard set of details for the specified connections, including supporting documents for the worksheet to include in the EOR’s calculations package for submittal to the jurisdiction having authority.
ConXtech moment frame collars are used in a typical ConXtech space frame building to provide a lateral force resisting system and typically comprise a little less than 50% of all columns in the building. The other columns and beams that make up the steel in the building structure will not have collars. This gravity framing is comprised of columns and beams interconnected with simple shear connections at each end, and these gravity beams are detailed with ConXtech’s “lower and lock,” single row bolted shear connections. The gravity column and beam framing is used by default at all locations during ConXtech’s initial design, when the size of the composite simply supported beams and supporting columns are still being analyzed. Selected regions of the building near the extremities will be converted to the collar-connected moment framing as needed during the design for lateral forces, with the objective of optimizing both cost and erection speed.
ConXtech systems enable structural engineers to specify pre-detailed shear connections from design tables provided by ConXtech at all non collar joints to maximize efficiency on construction projects.
A full building design will include a combination of patented collar moment connections, ConXtech Gravity connections and many non-proprietary connections from the AISC manual as required by any given project. ConXtech will fabricate all components and erect the entire building structure, to ensure the type, location and quantity of ConXtech components offers the greatest potential for schedule acceleration on site.
If you’d like help contrasting a traditional approach to a steel building with a potential ConXtech solution, the company offers a free conceptual layout for any engineering team wondering how to “ConXify” their project in the early design phases, including a cost and schedule estimate (inquire here).
SECTION 2
SPECIFYING PREFABRICATION IS AN EARLY-PROCUREMENT DECISION
It is important to specify a ConXtech system early in design to reap the true benefits of the system, and to avoid excessive rework in the design process.
In the 2020 Dodge Analytics report, respondents found that early-collaboration procurement methods such as Design-Build and Integrated Project delivery “helped” or “helped significantly” on projects that utilized prefabricated systems and components.
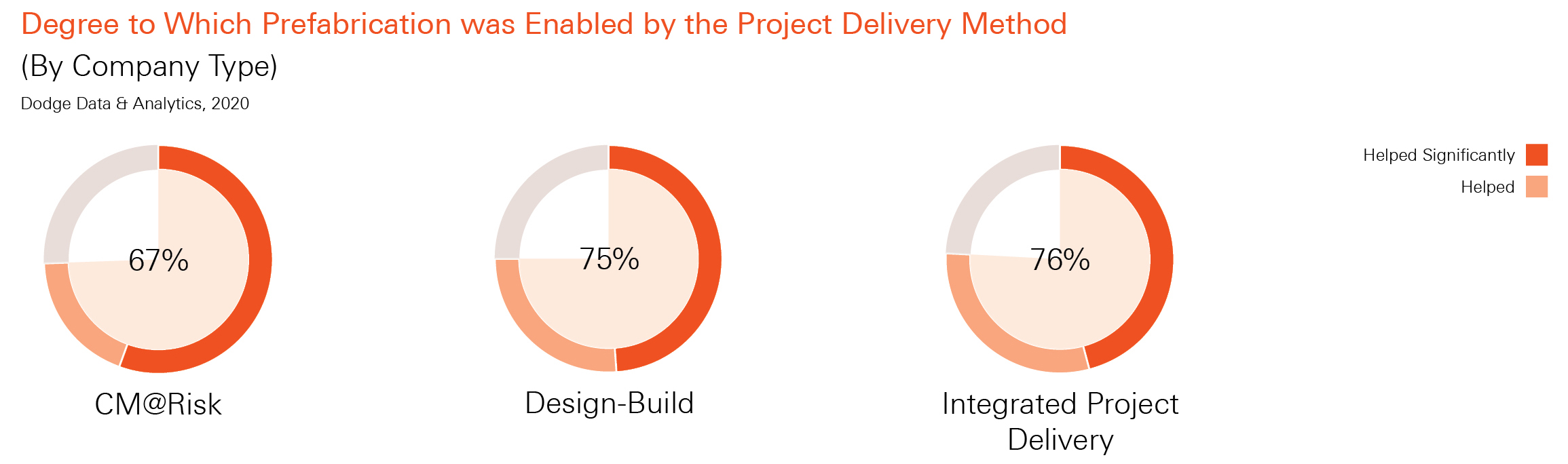
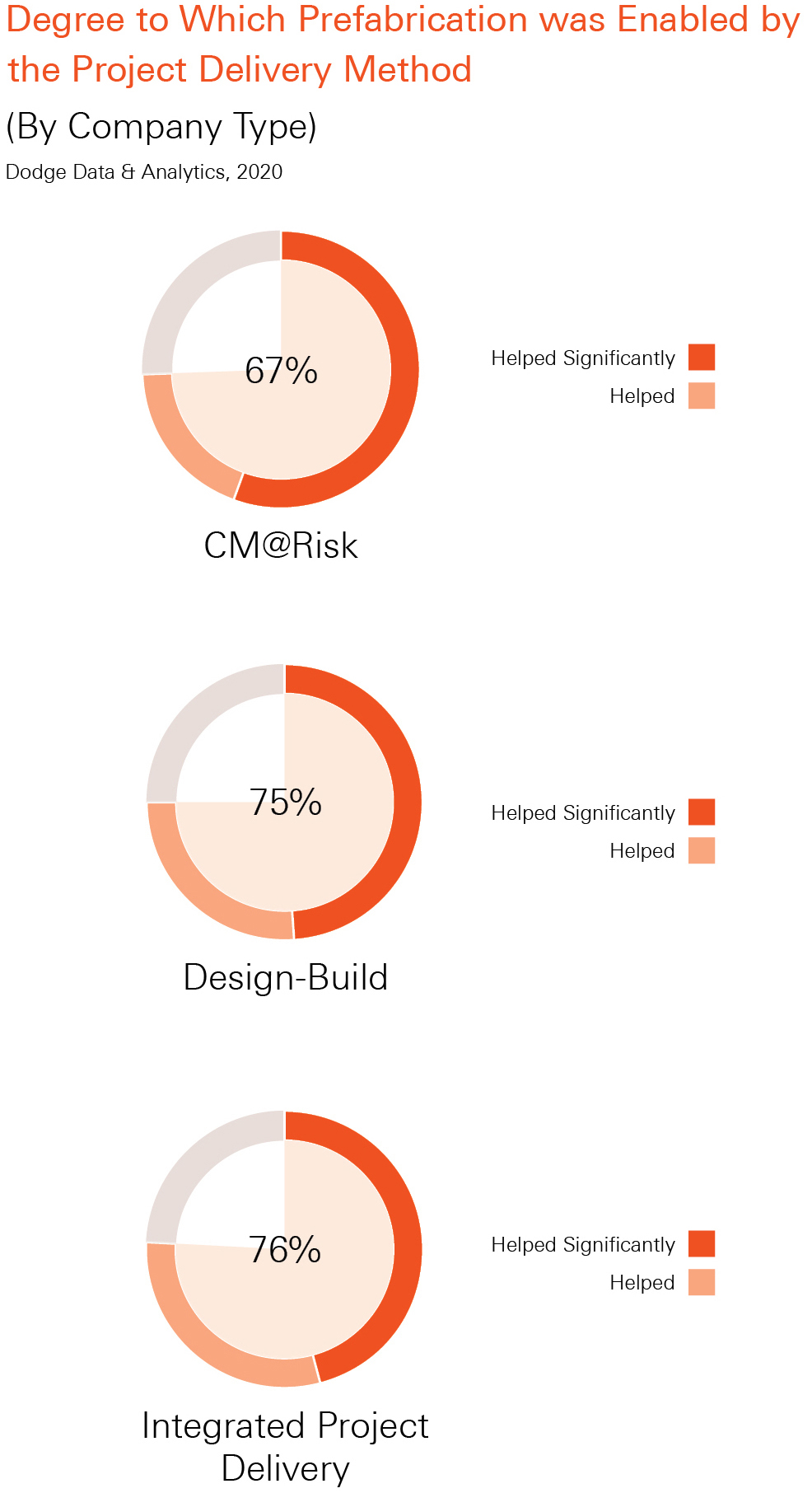
In a nutshell, the contract type should facilitate early-collaboration and engagement with the design team, in order to align best practices. The same study reports that the number one and two obstacles to increased use of prefabricated systems is late selection or project delivery methods that don’t enable such early coordination.
Introduction of the system as early as the Conceptual Design phase makes a pre-manufactured system most viable. For ConXtech, early engagement gives its engineers an opportunity to provide critical design input when it matters most, and when it can effectively maximize efficiency of manufacturing and erection. Once the design of a building is complete – it is often very difficult to retroactively fit-out a prefabricated system such as ConXtech without significant adjustment and redesign. In short, if an owner is curious about the advantages of using the system, consideration will be most fruitful during conceptual or early schematic design.
Top Obstacles Preventing Increased Future Use of Prefabrication and Modular Construction
(Index Based on Responses for Next 3 Years)
Dodge Data & Analytics, 2020
Survey participants selected their top three most important from a list of factors that are preventing increased future use of prefabrication and a separate list for modular construction. Numbers in the charts reflect an index created from these responses.
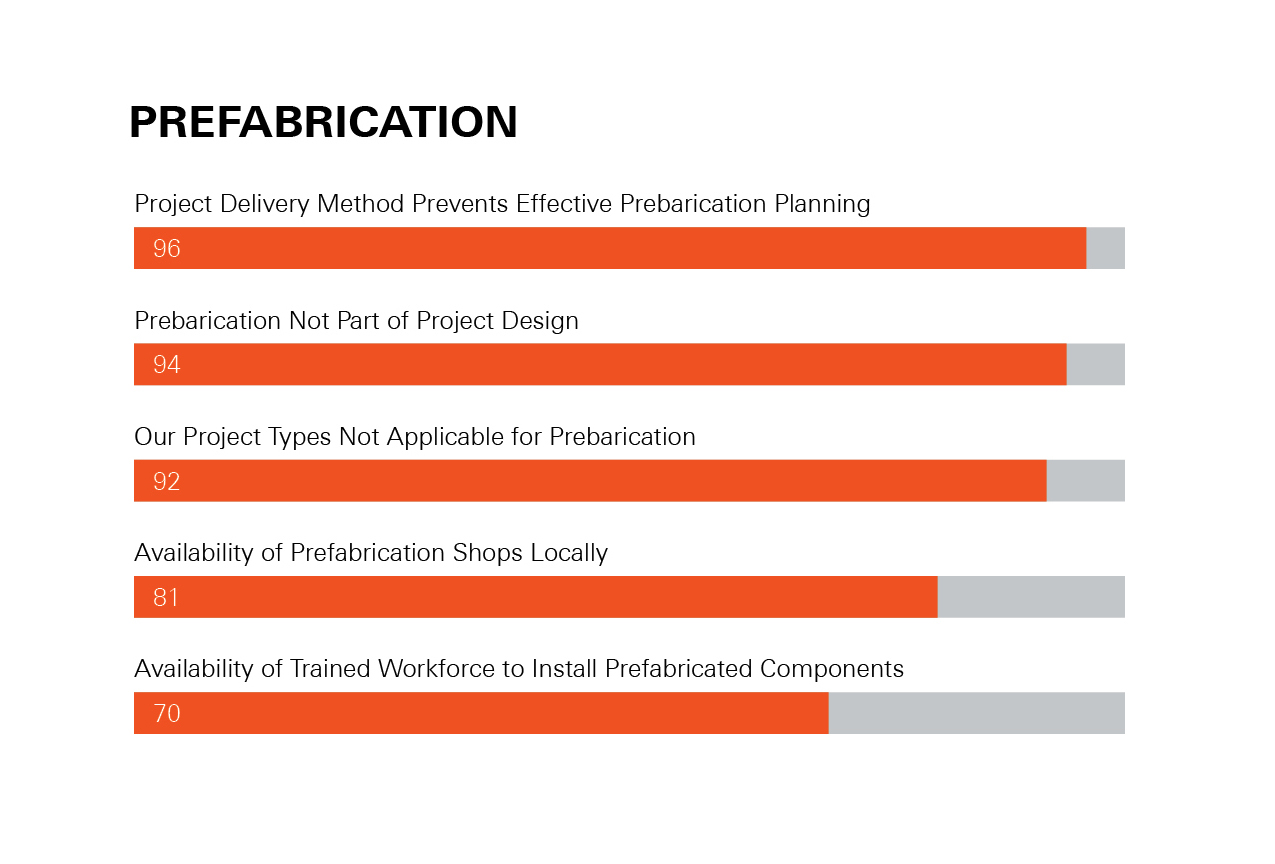
Engaging with ConXtech
ConXtech is a turnkey, manufacturing-enabled steel subcontractor with its own product engineering team. The company provides design-assist services to engineers that have been developed over years of process improvement in both the factory and on the jobsite.
When specifying a ConXtech system, design consultants engage directly with ConXtech engineers for fabrication and constructability input. ConXtech engineers can iterate conceptual drawings and optimize the design for real-world performance and jurisdictional approvals. Periodic reviews with the ConXtech team can help the EOR identify both challenges and opportunities for more efficient fabrication and erection. While final design decisions reside with the EOR, consultation with the fabricator ensures that engineers make real-world-informed decisions. If you have questions about where and how to start this process, drop the company an inquiry here: info@conxtech.com.
SECTION 3
PROJECTS THAT LEVERAGE CONXTECH STRENGTHS
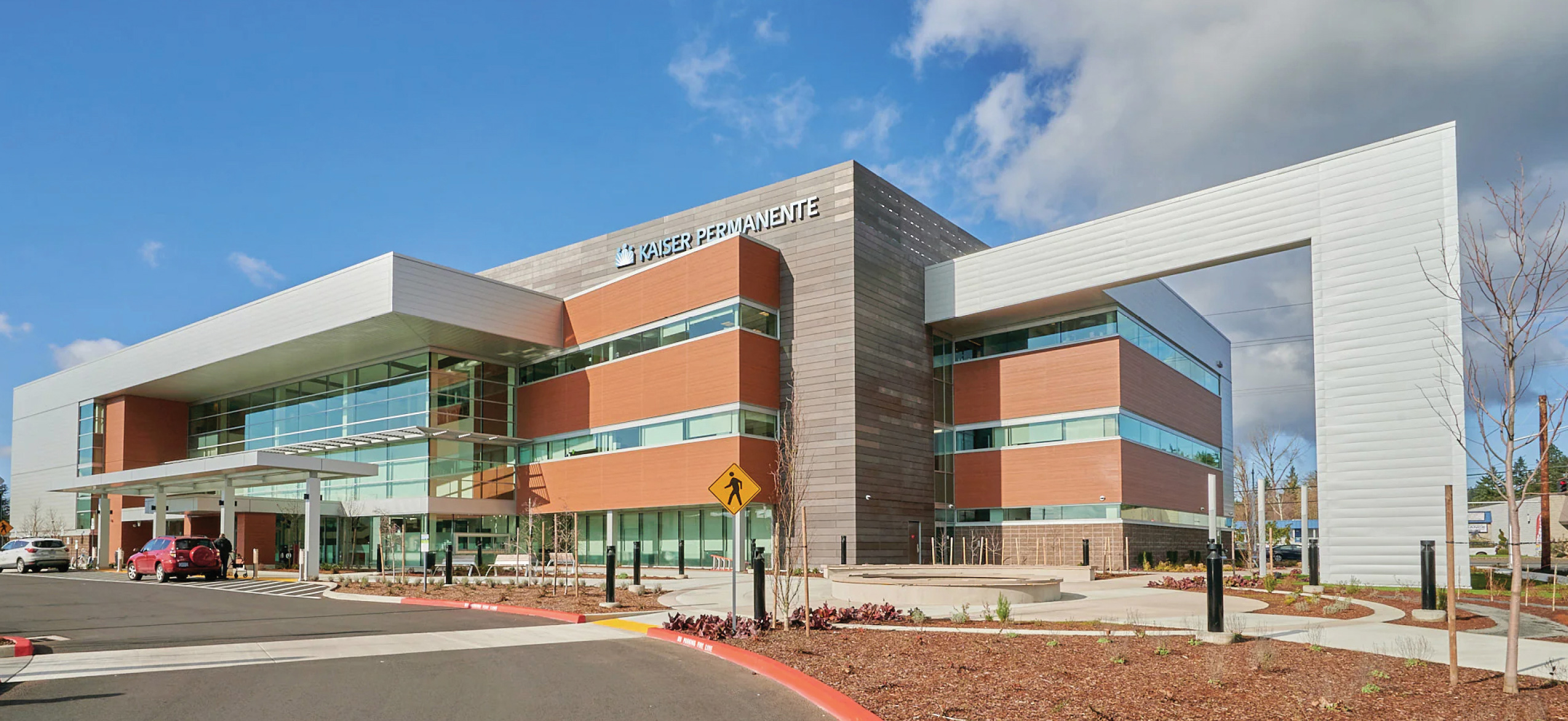
Projects that Leverage ConXtech Strengths
Where ConXtech really excels is when used in mid-rise rectilinear buildings that are at least 50,000 square feet. This is where the efficiencies of using a ConXtech system really shine compared to conventional steel construction. Depending on which system is used and the details of the building, crews can erect as much as 10,000-15,000 square feet of steel per day.
Buildings from 2 – 8 stories see some of the most significant schedule gains. Due to its full-eight erection, ConXtech systems don’t have the same delays erecting floor-to-floor as conventional methods. The system offers advantages for any project wherein construction schedule will meaningfully impact project economics. More categorically, a ConXtech system is well suited for:
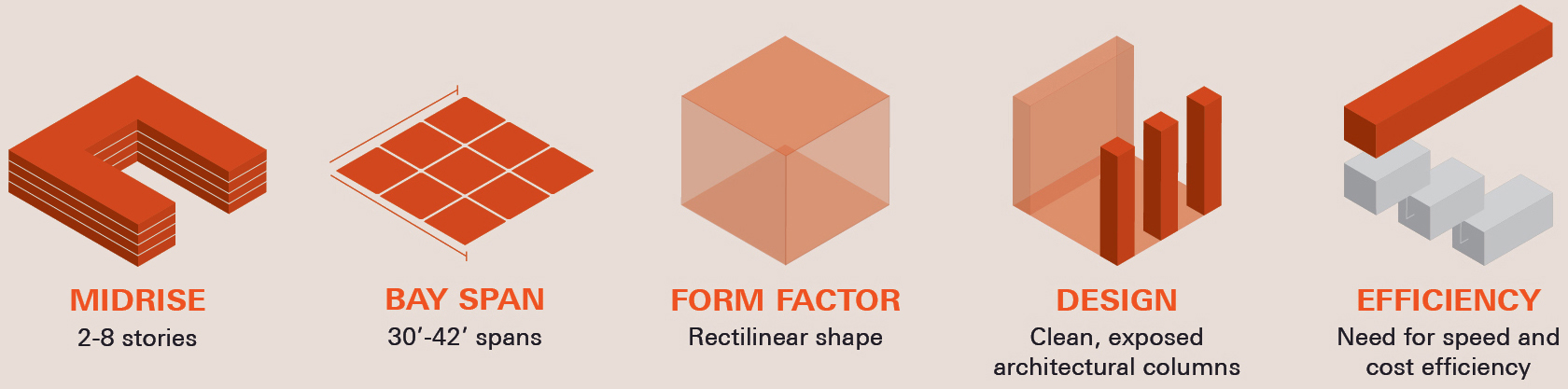
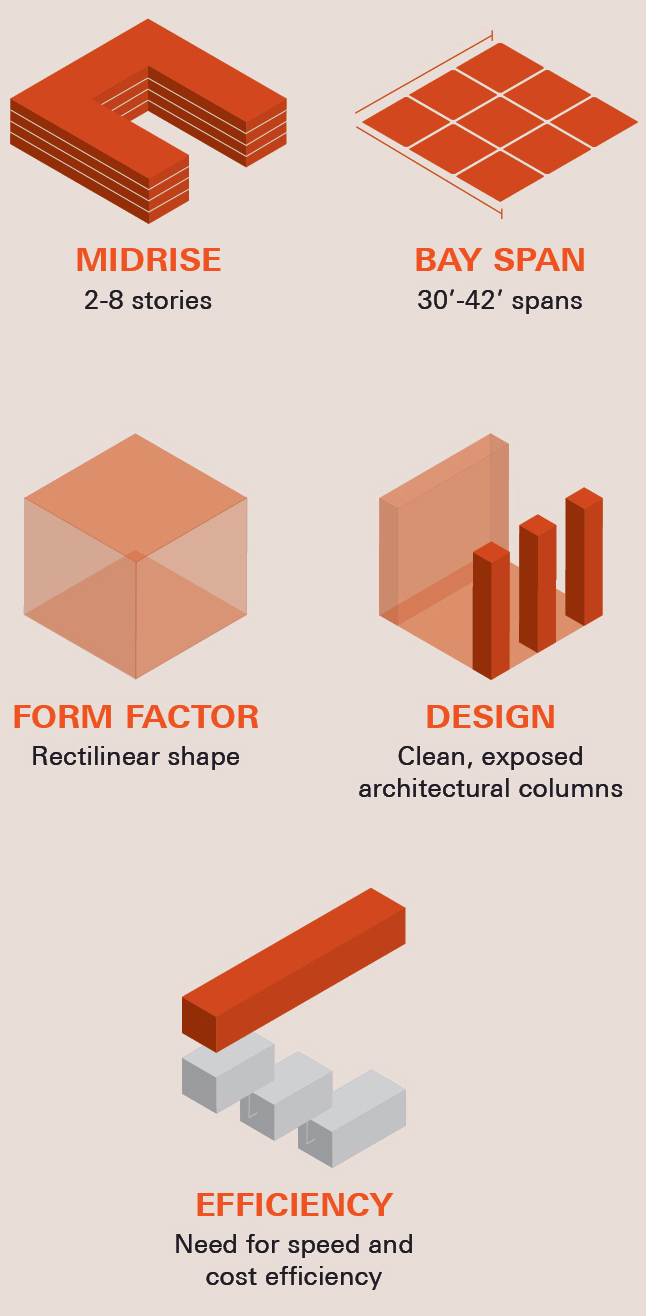
SECTION 3
PROJECTS THAT LEVERAGE CONXTECH STRENGTHS
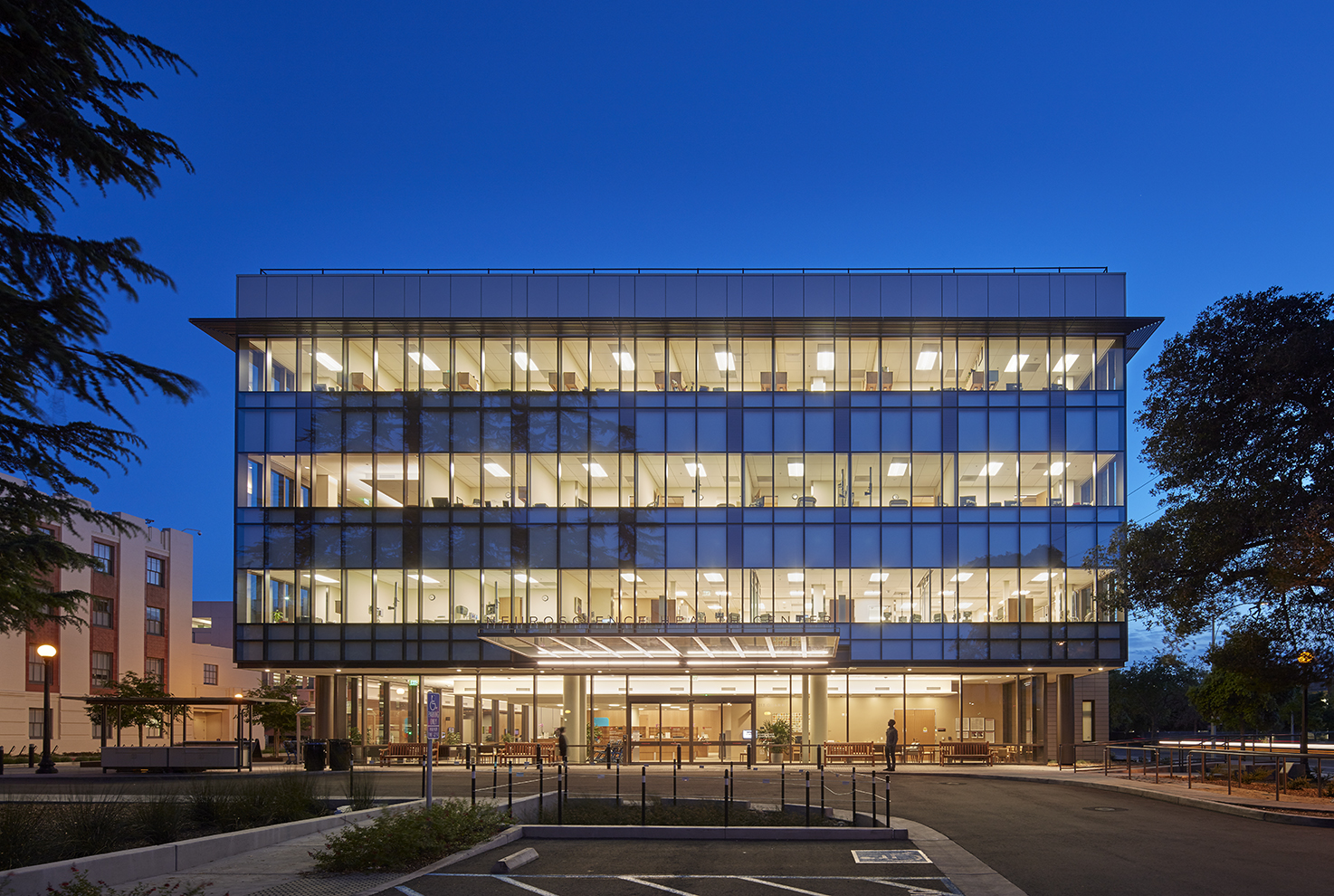
Stanford Neuroscience
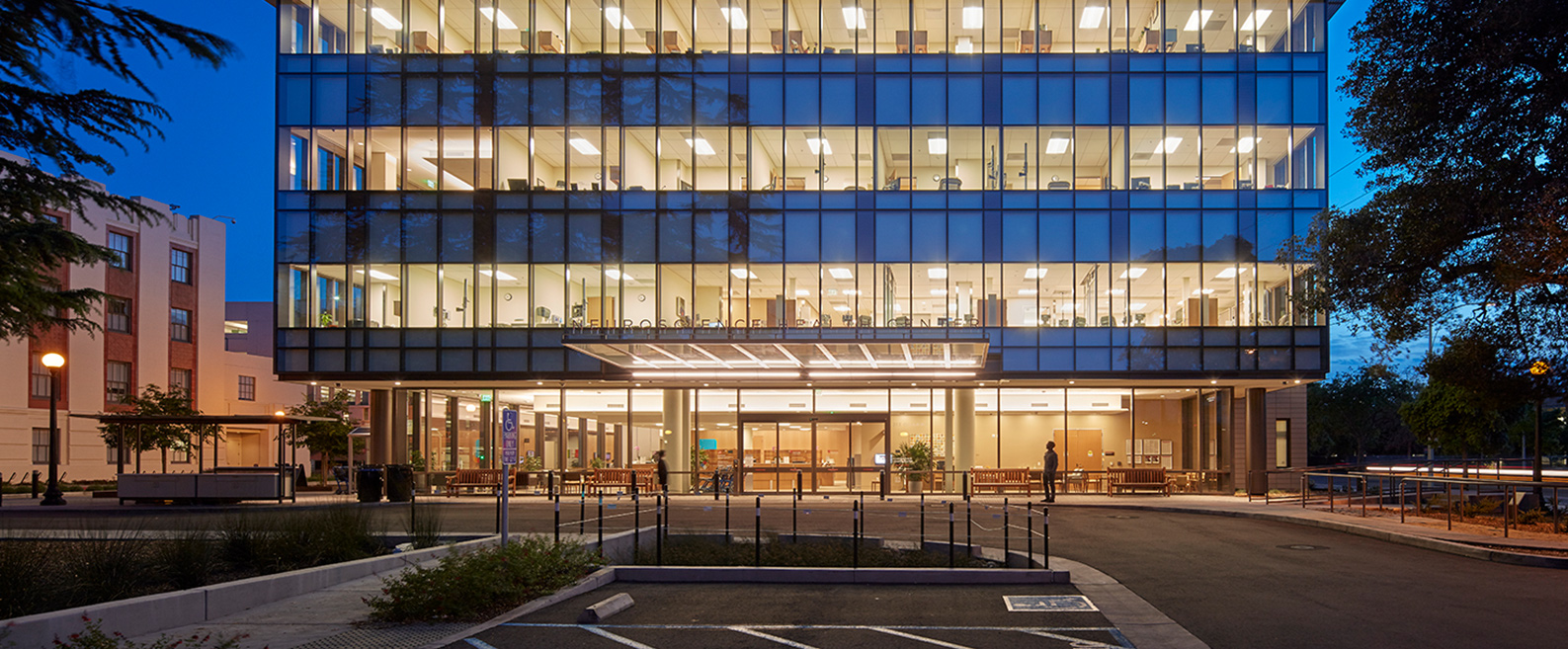
Stanford Neuroscience
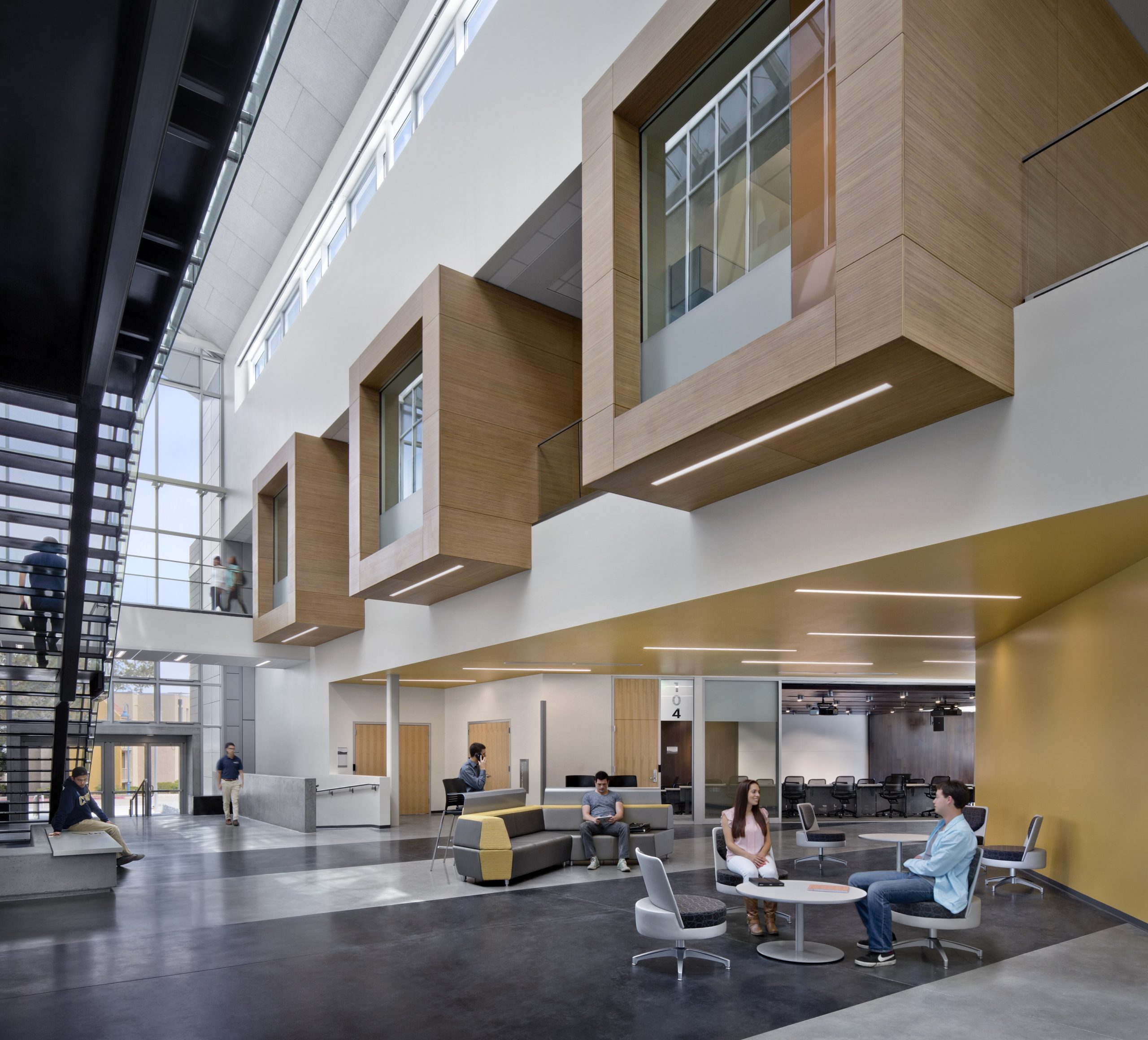
Southwestern College
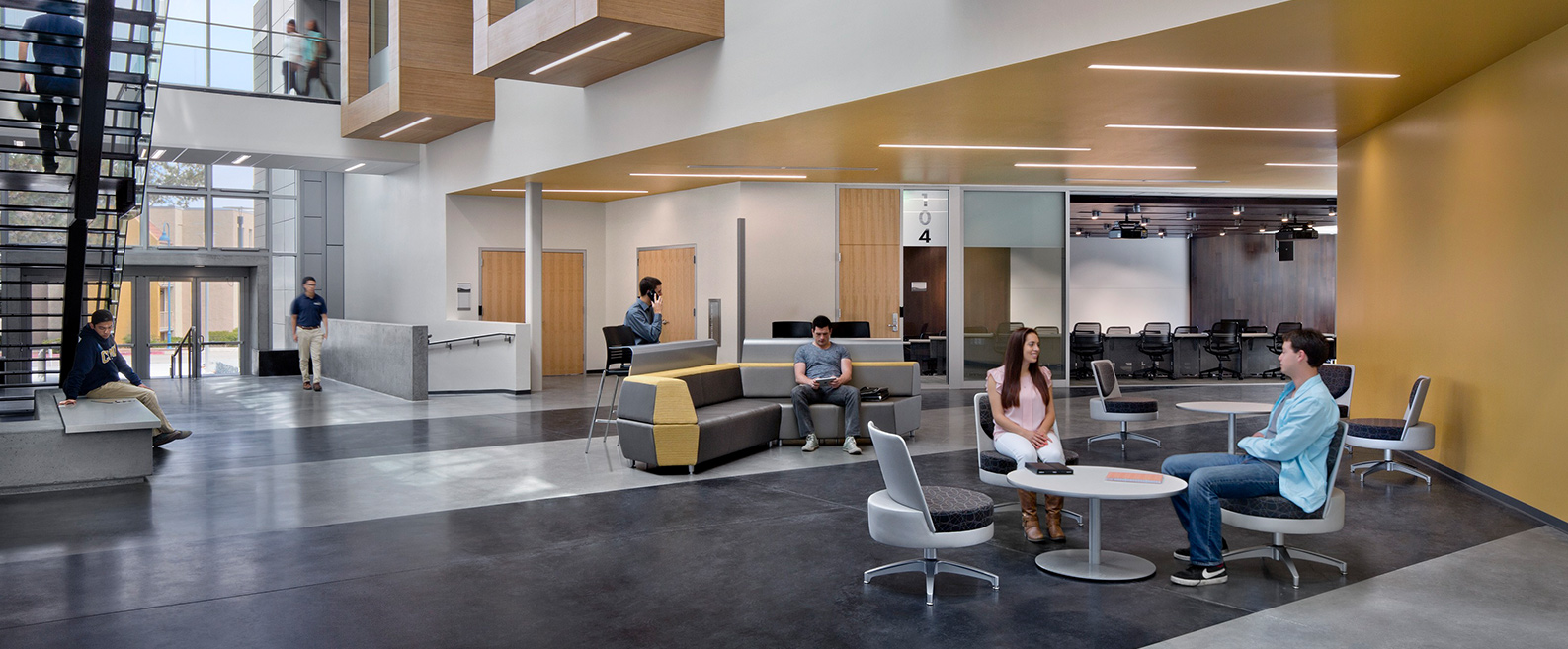
Southwestern College
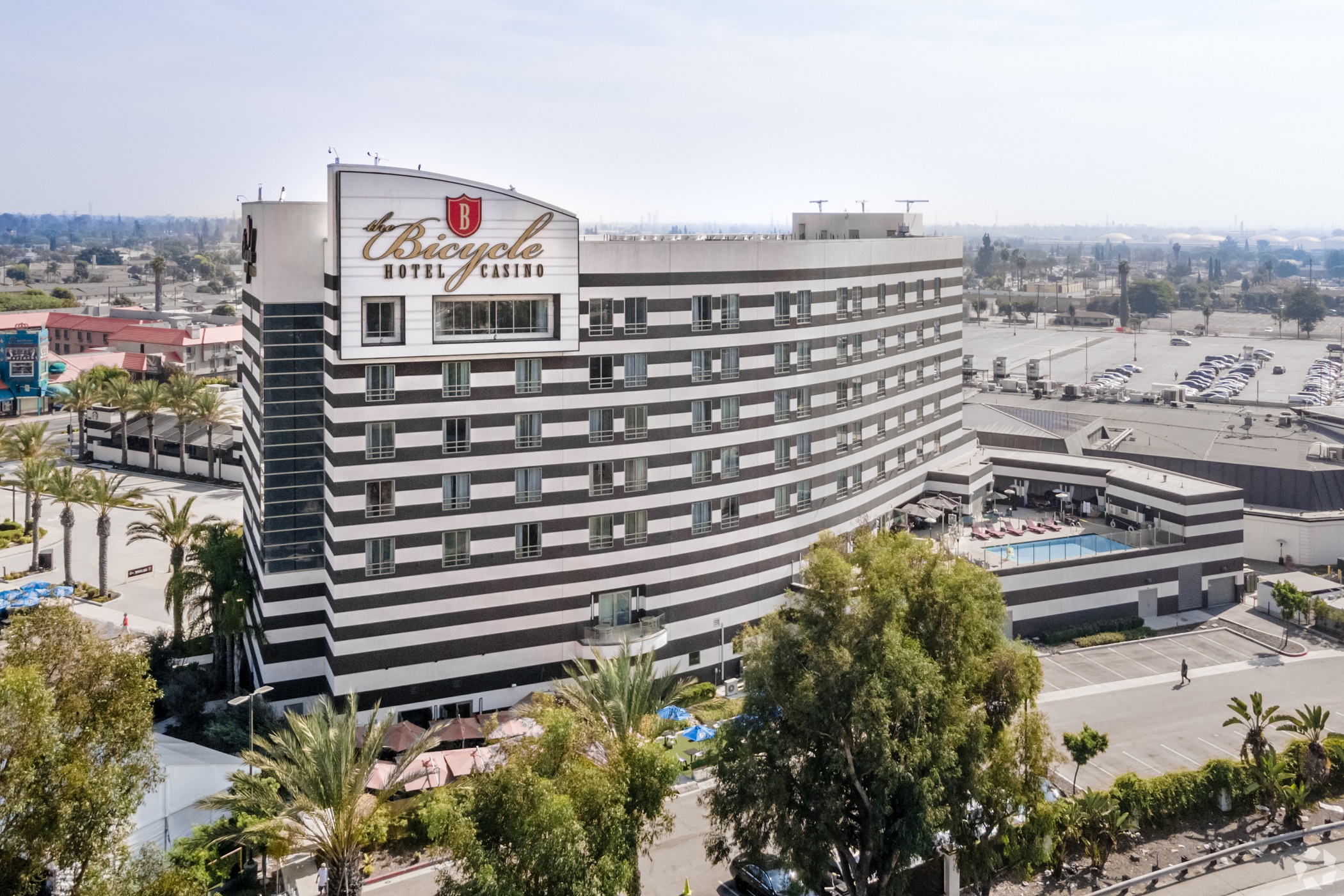
Bicycle Club Hotel & Casino
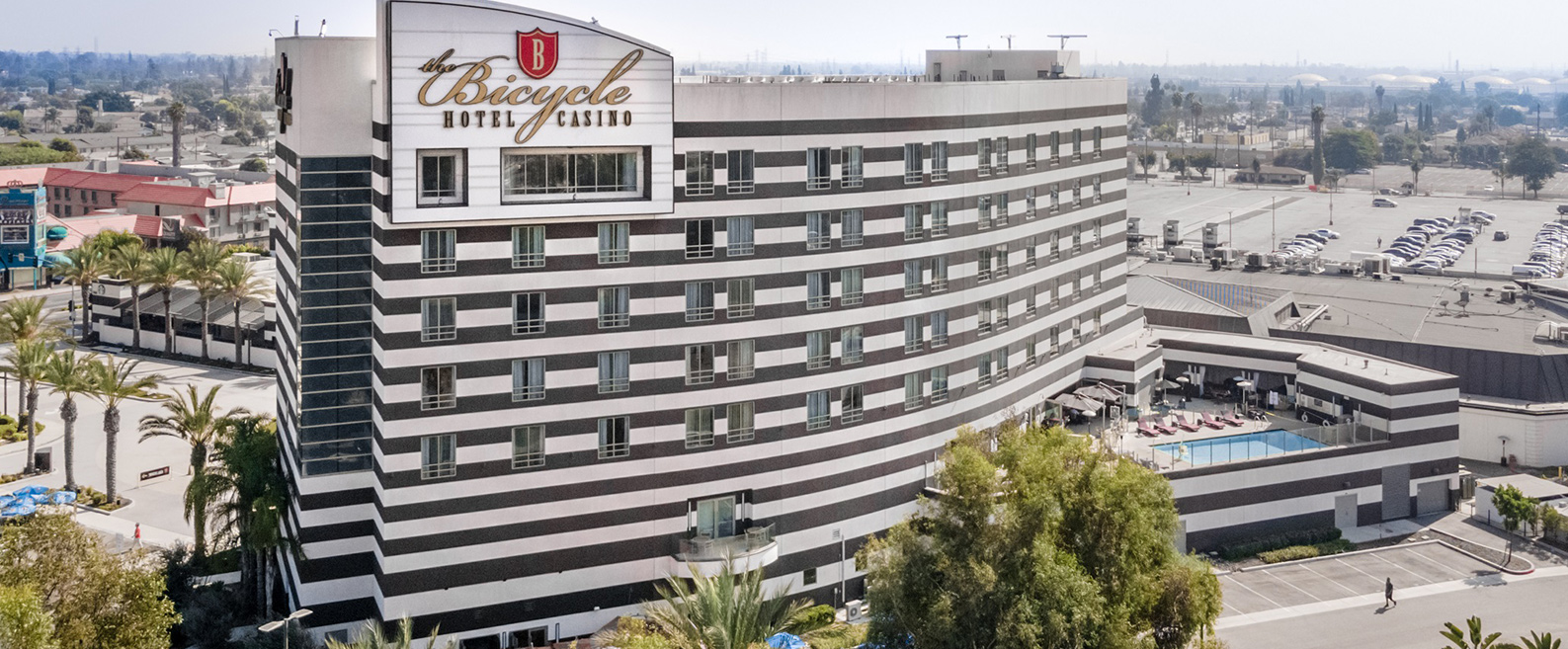
Bicycle Club Hotel & Casino
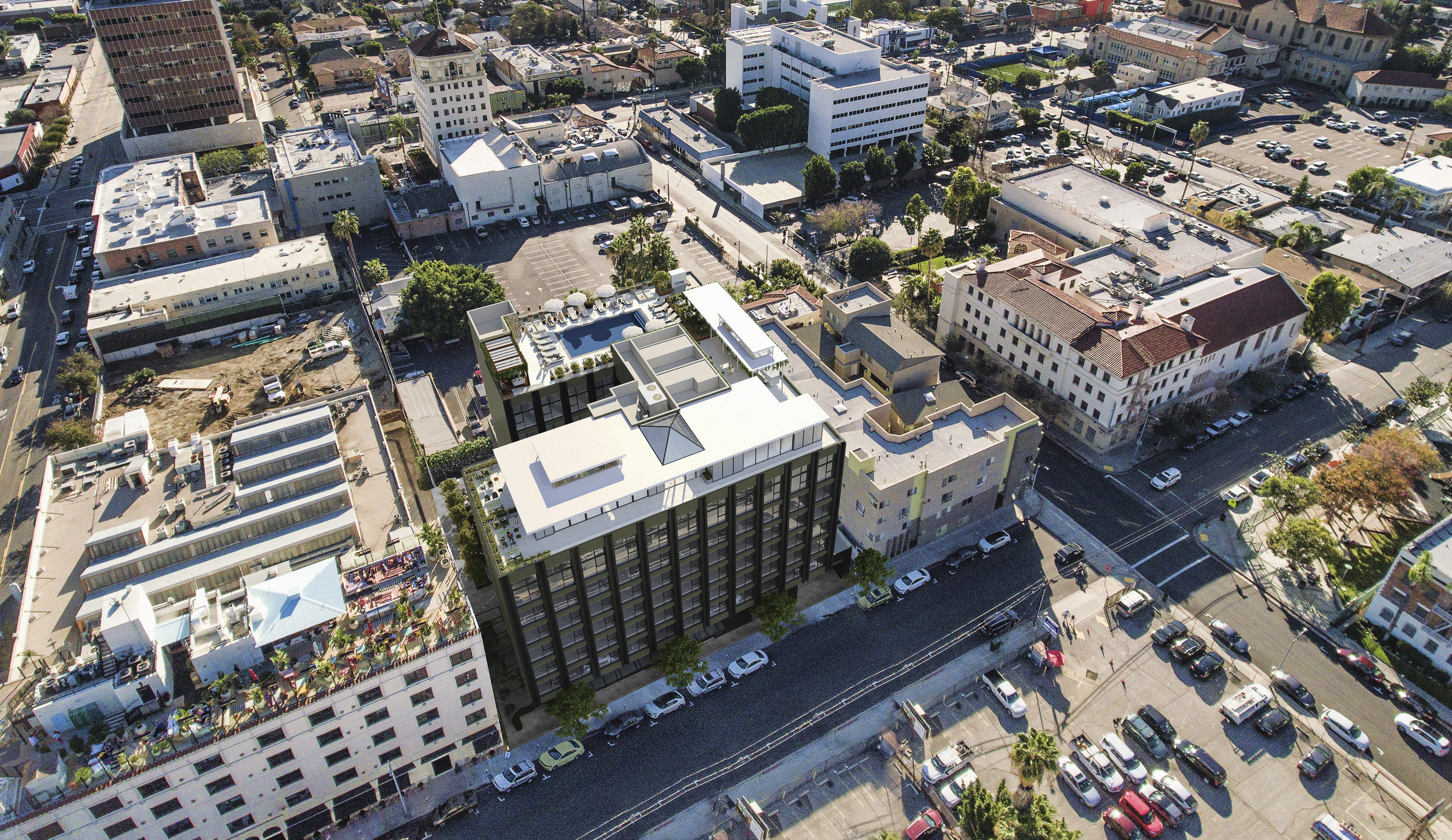
Selma Tommie Hotel
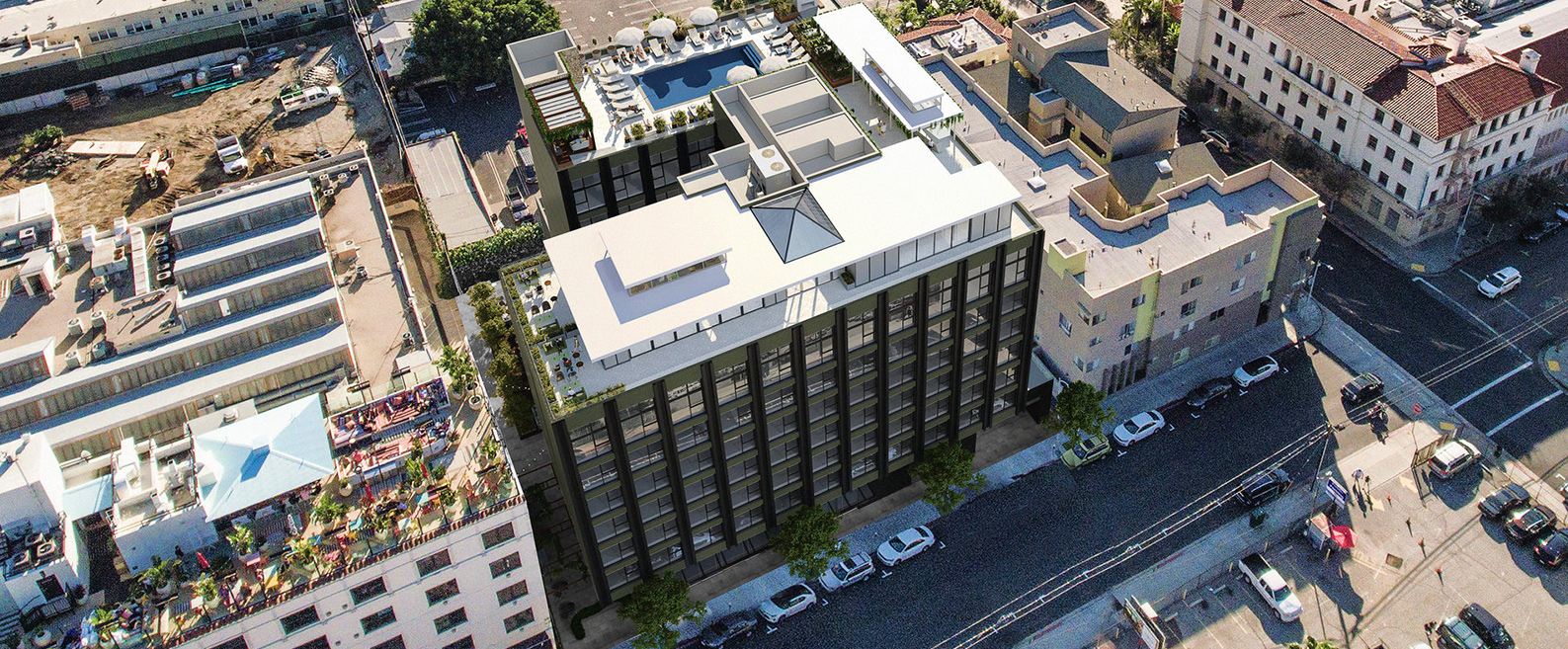
Selma Tommie Hotel
Projects that Leverage ConXtech Strengths
Flexible Office/Lifesciences/Laboratory: Between the CONXL300 and CONXL400, ConXtech offers a standard grid from 12’-45’ between columns, making it almost infinitely suitable for any sort of flexible office space.
Healthcare: Chapter 22A of the California Building Code provides an exception allowing ConXL400 bolted special moment frames in HCAI administered, OSHD building types OSHPD 1, 1R, 2, 4, and 5.
Architectural Expression: Thanks to clean columns and prefabricated collars, the ConXtech system is often expressed as part of the interior architecture.
Hotels: The spatial discipline of hotel room grids, coupled with the outsized impact of early revenue makes them a natural fit for ConXtech. Primarily the CONXR200, with its smaller column and beam sizes, is suited for the room portion of a hotel.
Small/Regional Airport: The long beam spans and rapid installation of the CONXL400 means a small airport terminal structure and ceiling volumes up to 18’ high can be erected in less than two weeks.
Education/Student Housing: School campuses are some of the most challenging sites for construction, given safety concerns and intolerance for learning disruptions. A ConXtech crew can complete structural erection during even a short school break, eliminating crossover between heavy steel trades and student activity on campus.
Data Center/Mission Critical: The intense schedule pressure, paired with the architectural simplicity of most data centers make them an ideal project type for which to consider a ConXtech steel solution. On a recent 136,000-sf data center in Northern California, ConXtech was able to erect the entire 2-story structure, including roof dunnage, in just 9 days and bring the finish trades into the building 3 months earlier than would have been possible using traditional steel framing.
Medical Office Buildings (MOB): In essence a specialty flexible office building, an MOB benefits from ConXtech for many of the same reasons as any flexible office space, with the added benefit that the onsite safety factor of the ConXtech system and method is unparalleled. With fewer crew members on site and 3x-5x fewer days to erect, personnel “at-risk” hours are exponentially diminished.
For these reasons, ConXtech has become a staple in the Medical Office Building sector and has been on the pre-approved procurement registry for Kaiser Permanente for nearly 15 years.
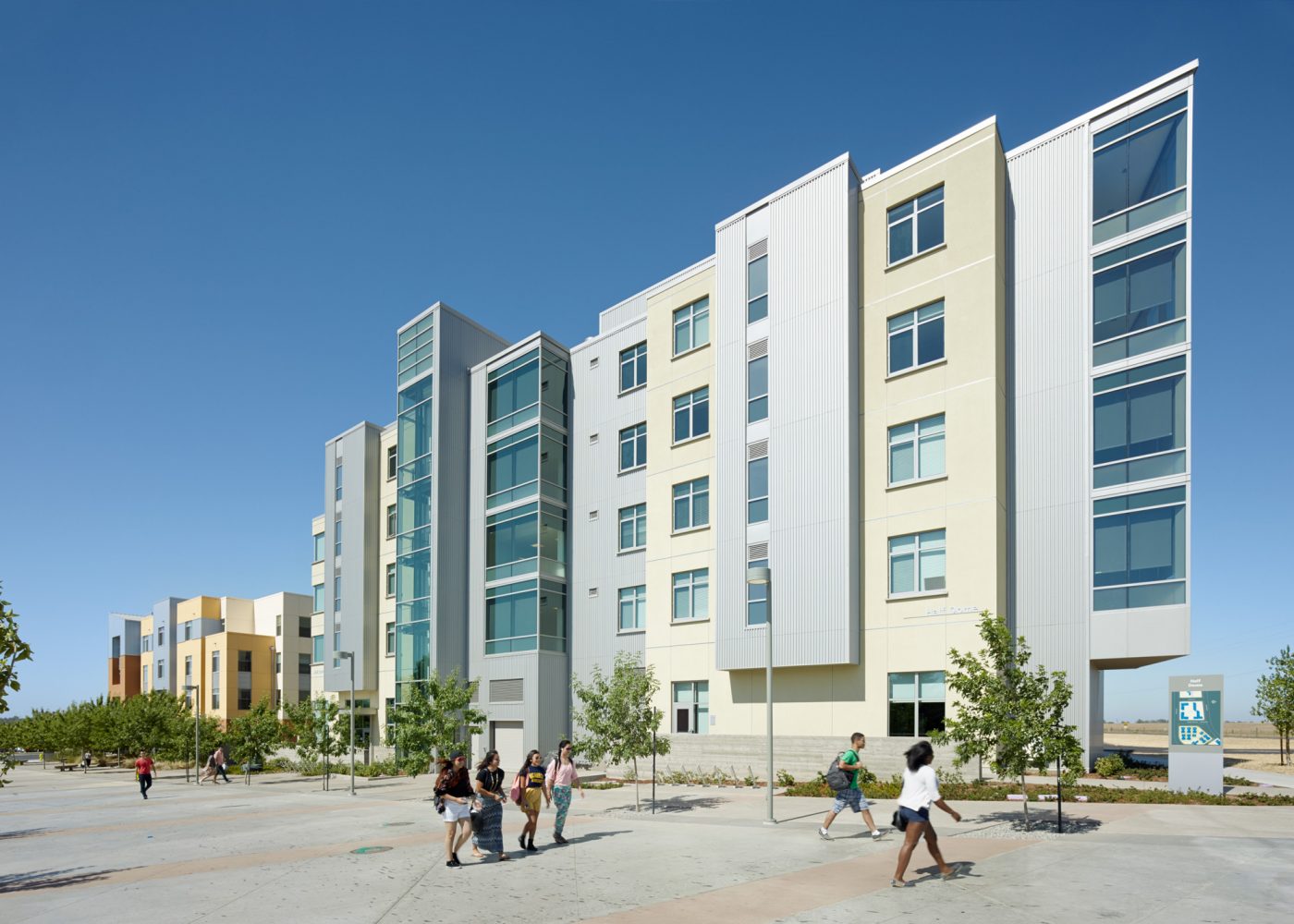
UC Merced Student Housing
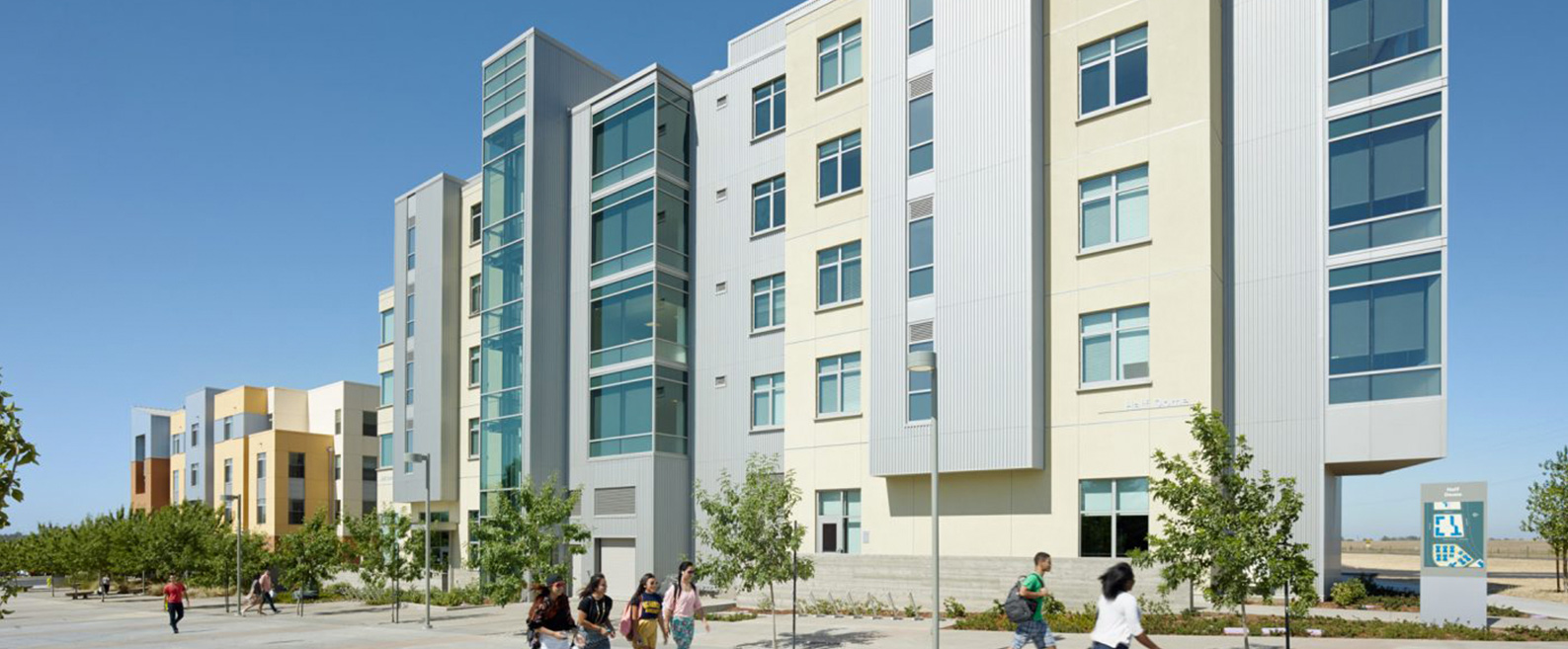
UC Merced Student Housing
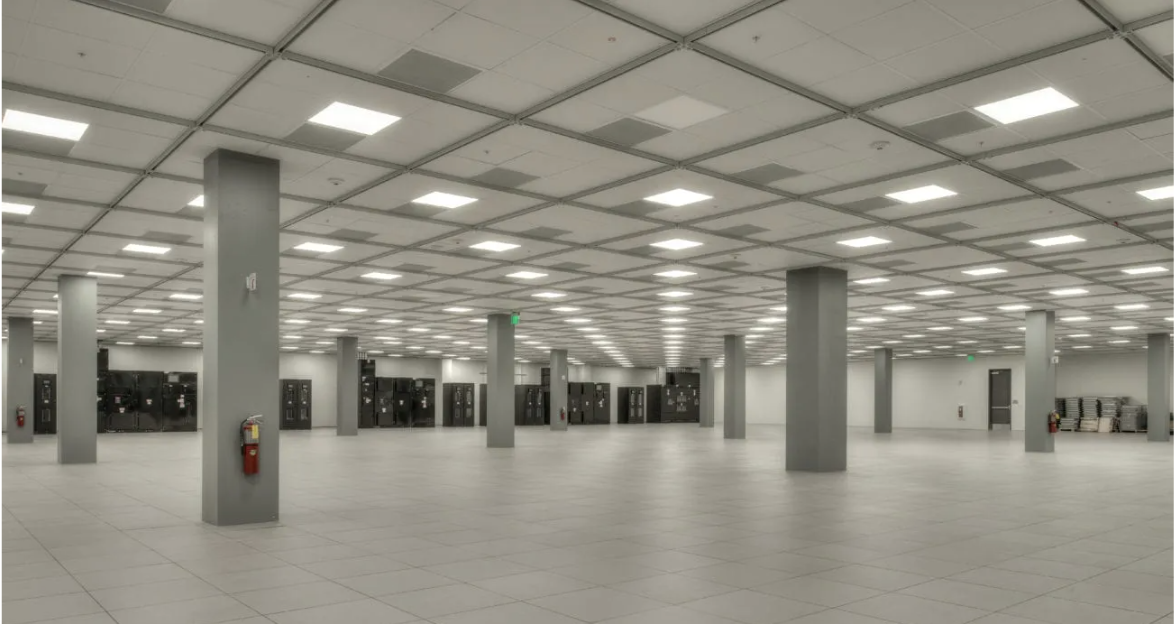
CoreSite SV7 Data Center
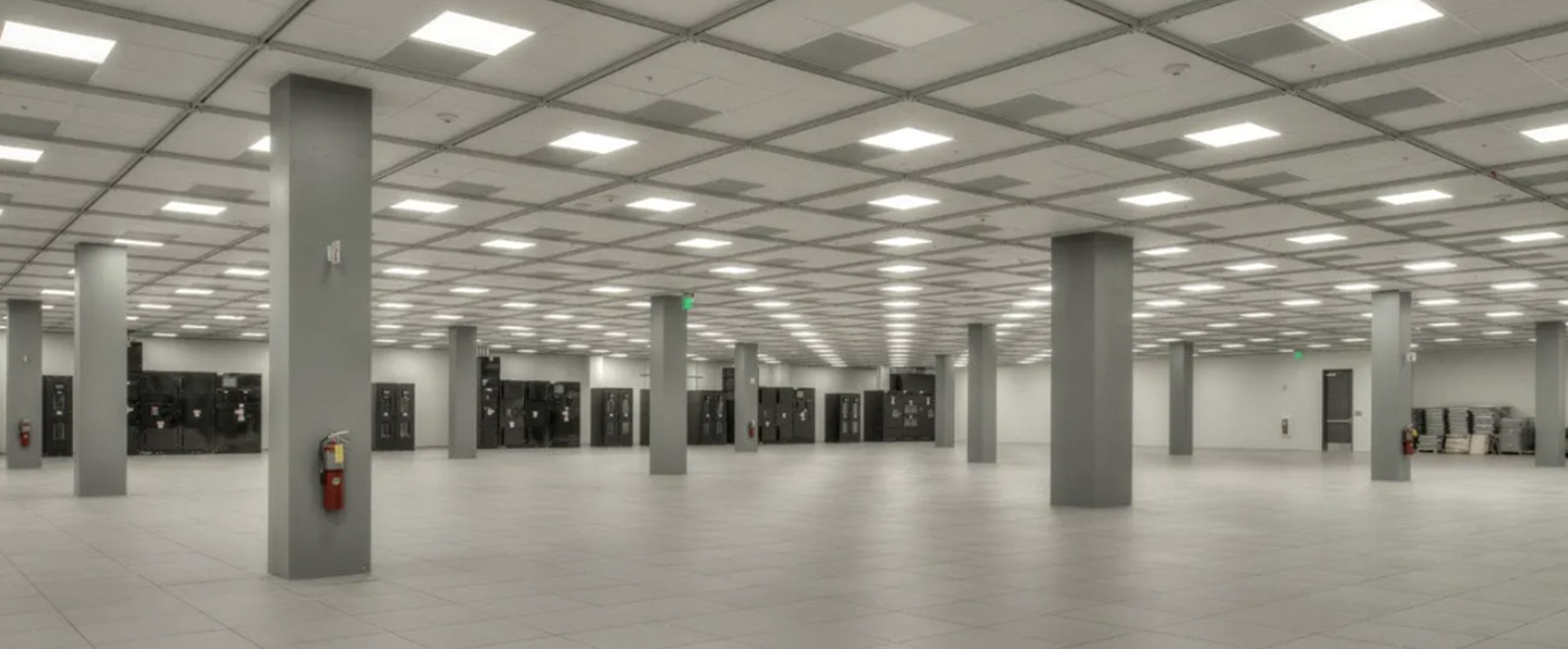
CoreSite SV7 Data Center
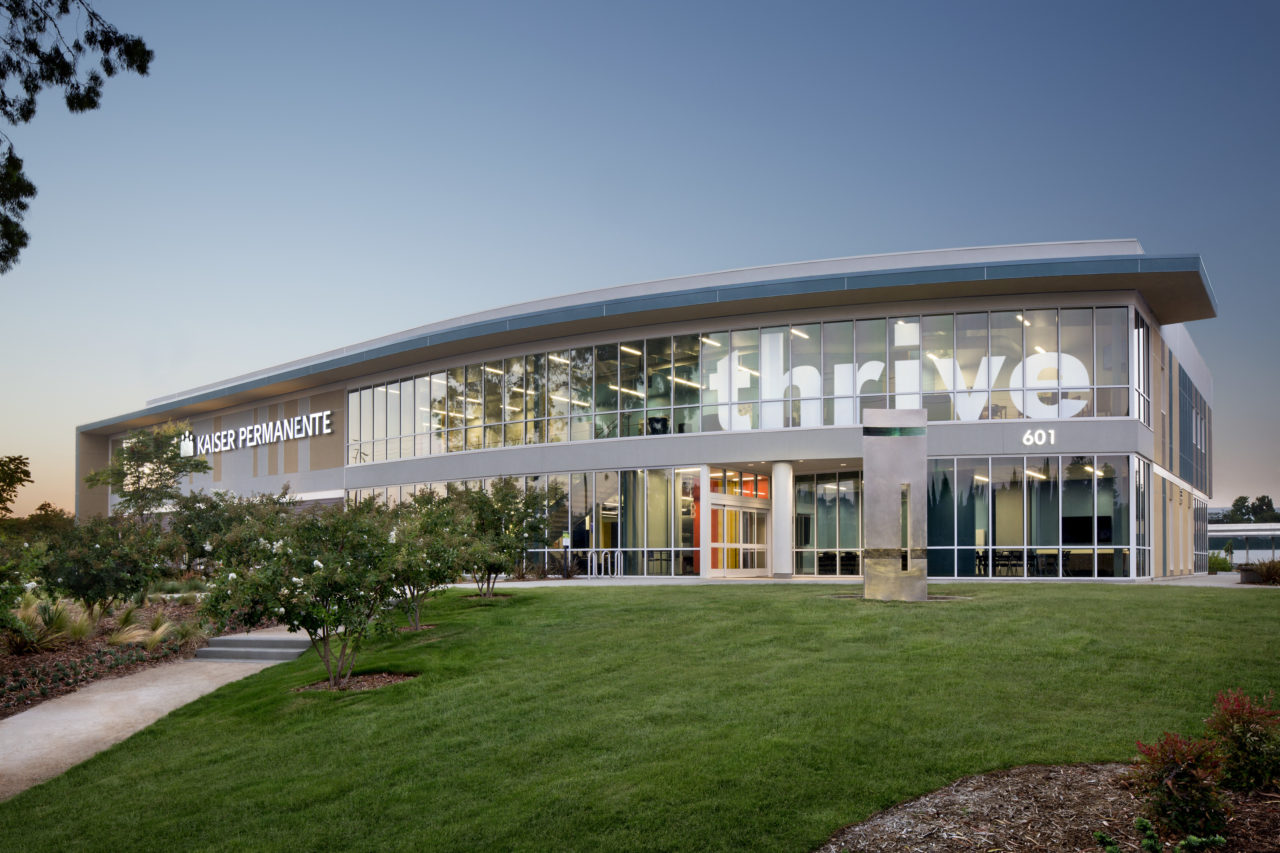
Kaiser Permanente MOB La Habra
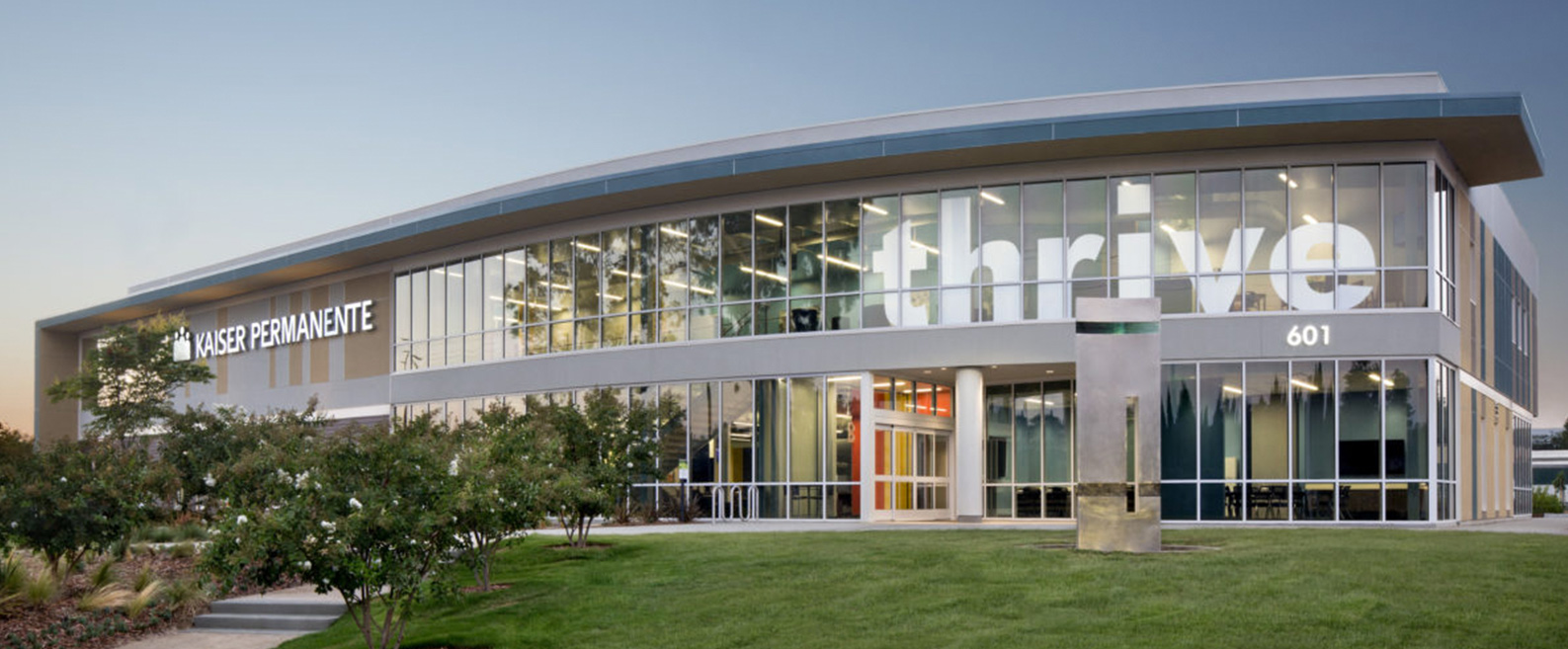
Kaiser Permanente MOB La Habra
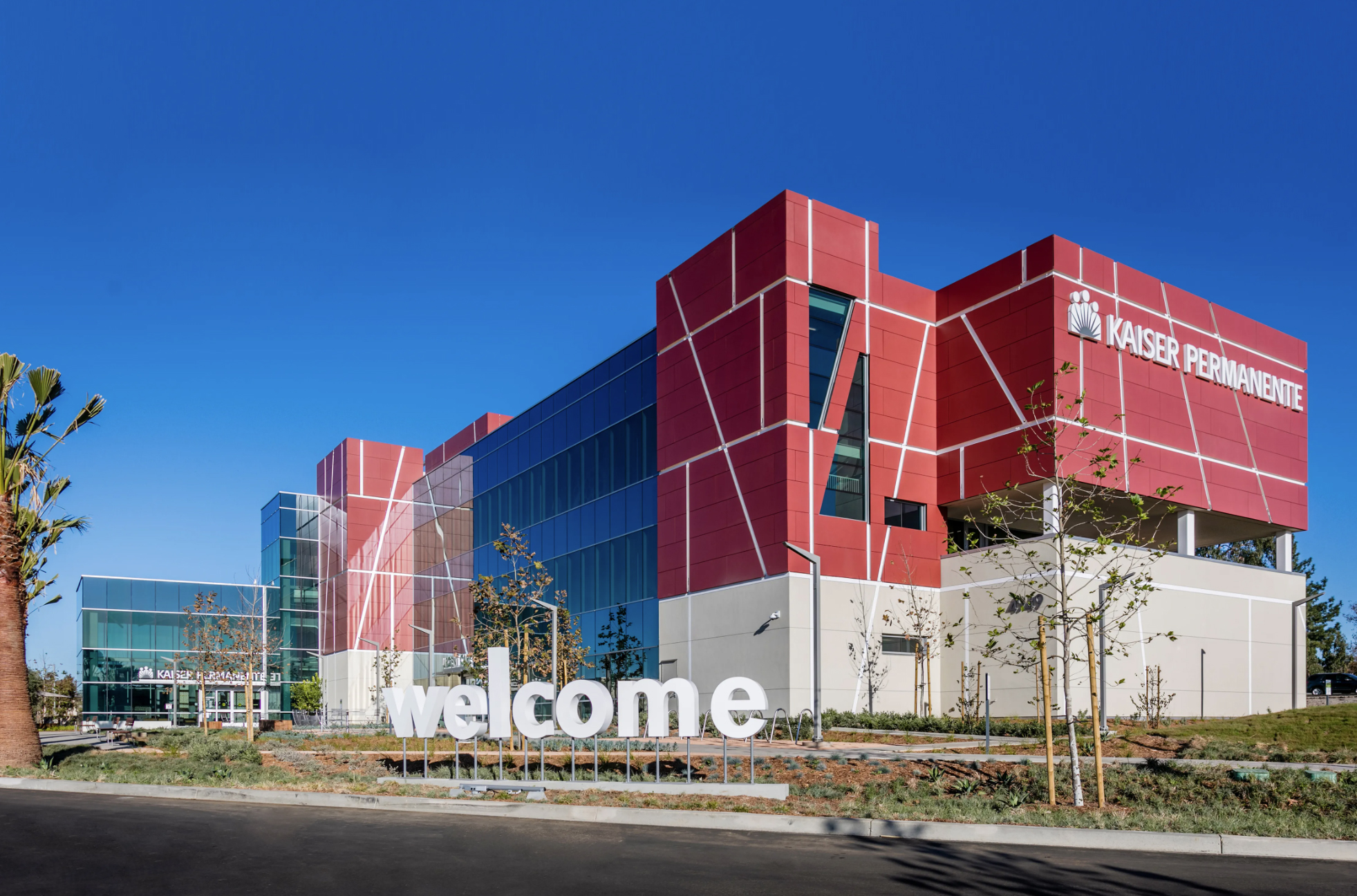
Kaiser Permanente Santa Rosa
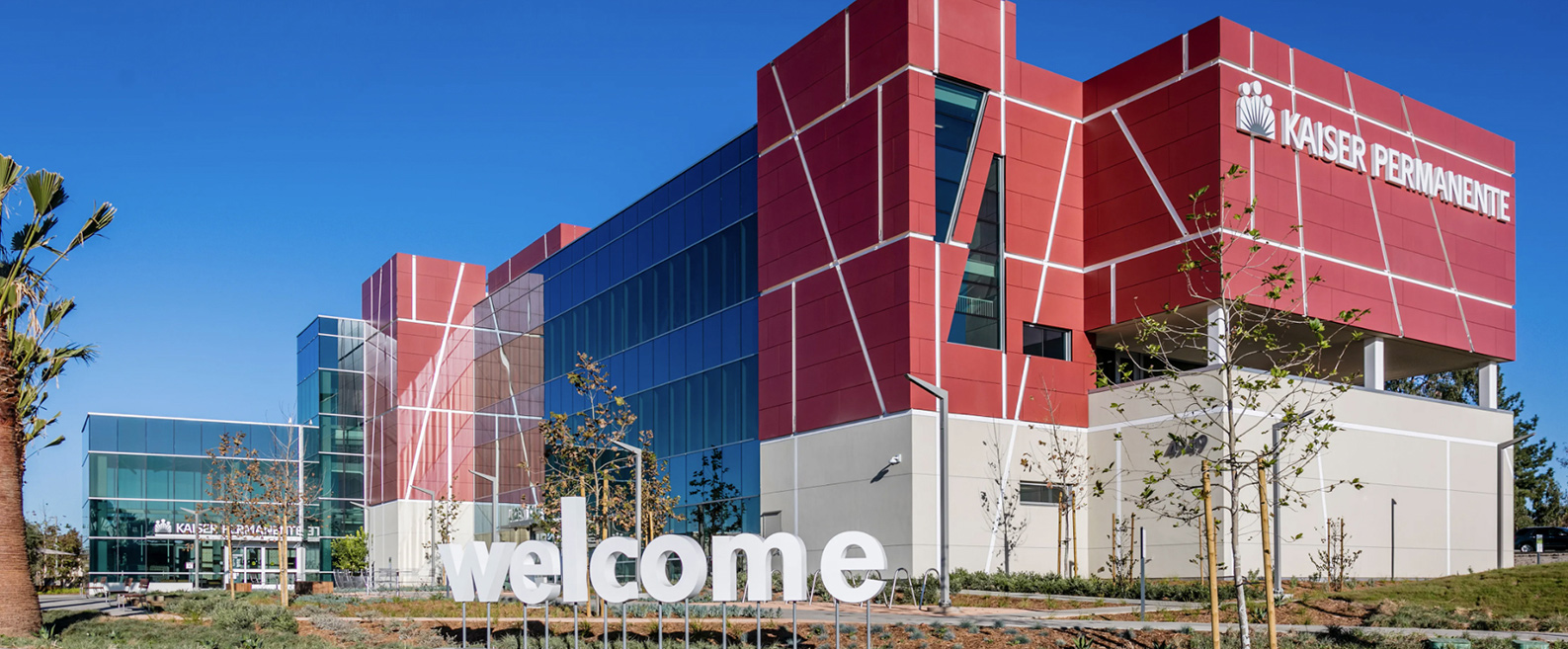
Kaiser Permanente Santa Rosa
SECTION 4
CONXTECH PROCESS IMPROVEMENTS OVER THE YEARS
LEAN from Off-site Manufacturing to On-site Erection. ConXtech Process Improvements over the Years
ConXtech’s patented connections are designed to make life easy for its crews on-site, and constant feedback over fifteen years has made both factory and field teams better over time. Here are a few of the specific tactical benefits the system has achieved over time:
The Lower and LockTM connections don’t require on-site welding, and the connections are designed to facilitate a meaningfully improved construction process in the field that helps general contractors move other trades into the building sooner.
Steel inspections are dramatically reduced on-site.
All ConXtech connections are “lower and lock” which provides instant stability, even prior to bolting. Because the structure can be stabilized during construction by the collars before bolting, crews can reduce interior cable bracing during erection of the primary frame.
A ConXtech prefabricated framing system is installed by workers standing on a fully planked elevated working surface while fully tied off and surrounded by a full-height safety rail. Unlike with a traditional steel erection method, using the ConXtech “lower and lock” details workers can set beams without exiting the safety of the railed work platform. The platform moves with the worker, eliminating the 30’ climbing height limit that restricts conventional steel erection. By avoiding the typical limitations, crews can erect the building to full height from bay to bay, safer and far faster than a comparable steel structure.
SECTION 4
SIMPLY FASTER: BY THE NUMBERS
Simply Faster:
By the Numbers
Brass tacks time…how much faster is a ConXtech implementation than traditional steel erection methods? ConXtech analyzed project data from the last 15 years of erecting the system, and then compared that data with that of average steel erection speeds on similar projects erected in a more traditional fashion. By comparison, on most projects steel erection using ConXtech was 3-5x faster than a comparative steel erection using traditional means, with the greatest differentiation on buildings of greater than two-stories. The charts below offer some insight into the magnitude of savings and the relative impact of increasing building stories vs. square footage. On the left, the ConXtech savings as stories are added to the building, with square footage held constant. On the right, the inverse – the building remains a constant four stories, and square footage is increased.
Savings vs Conventional
- Magnitude of savings is proportionate to magnitude of project
- On average, ConXtech is 67% faster
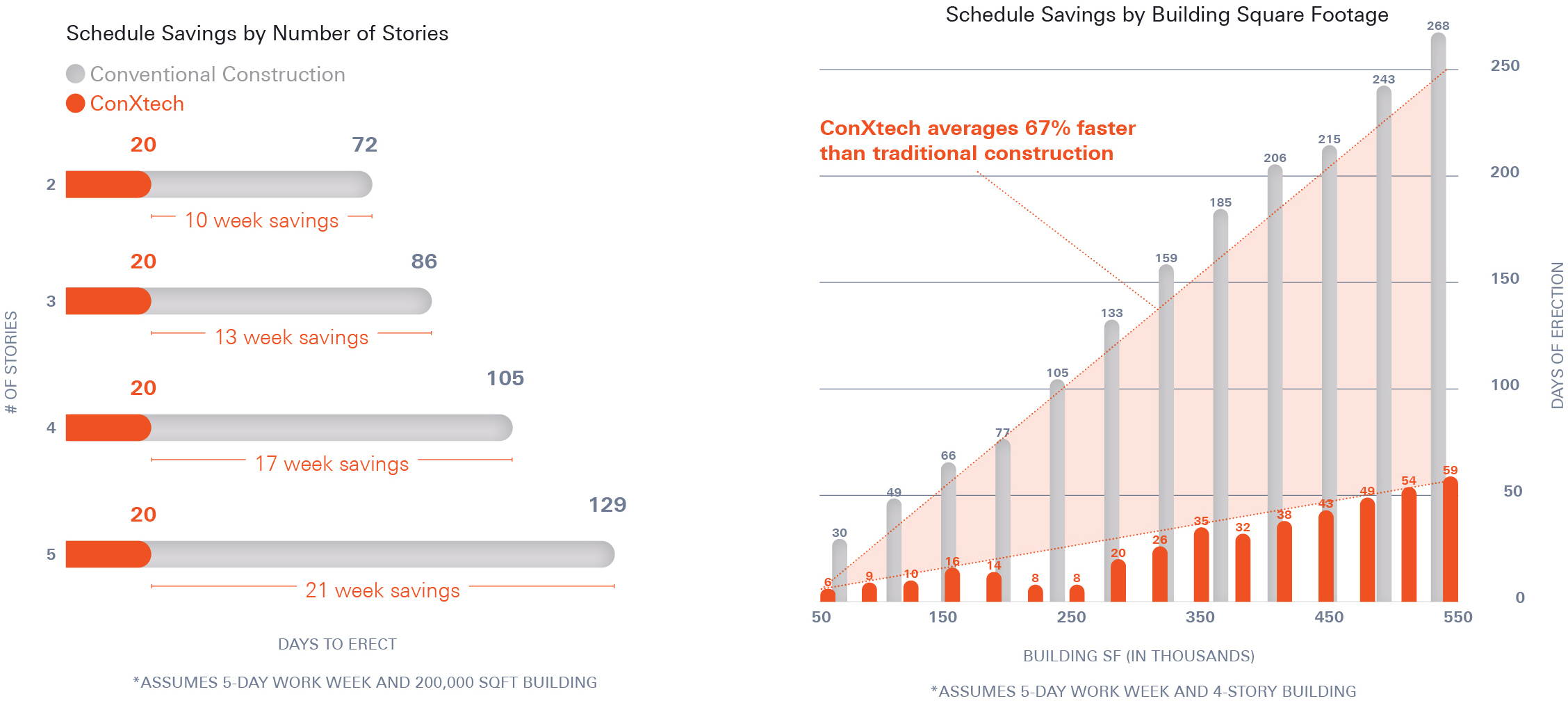
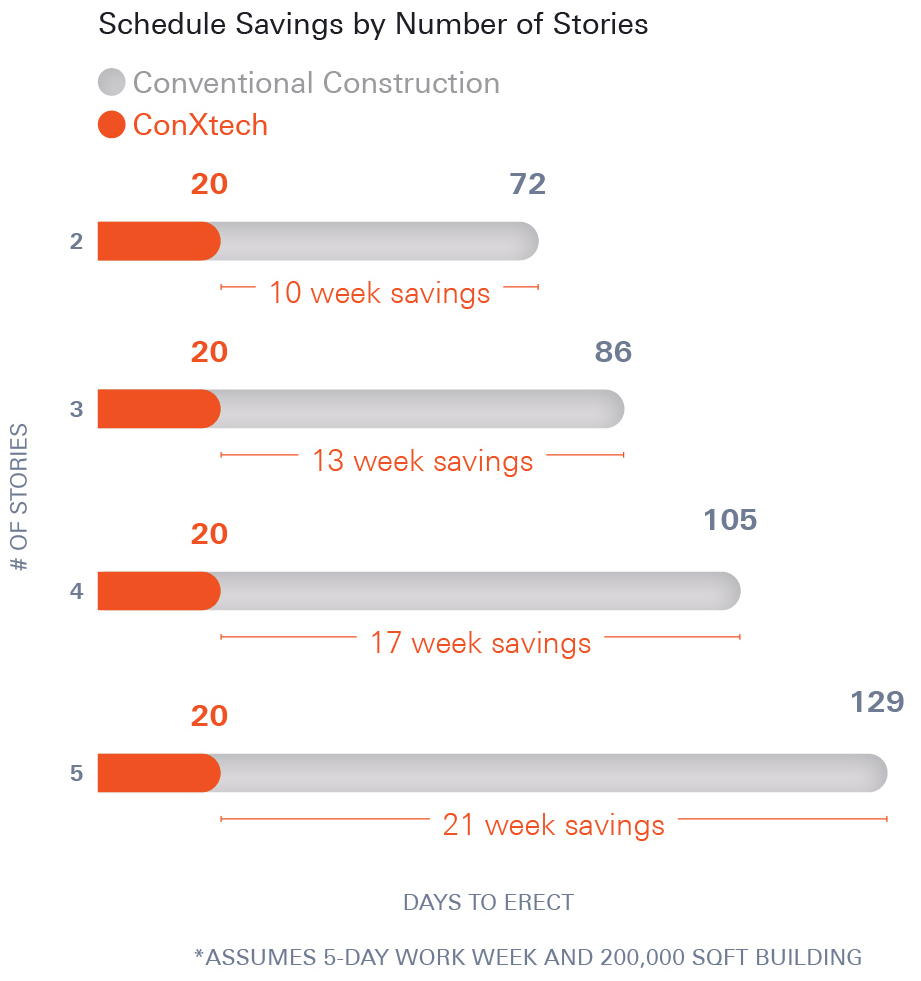
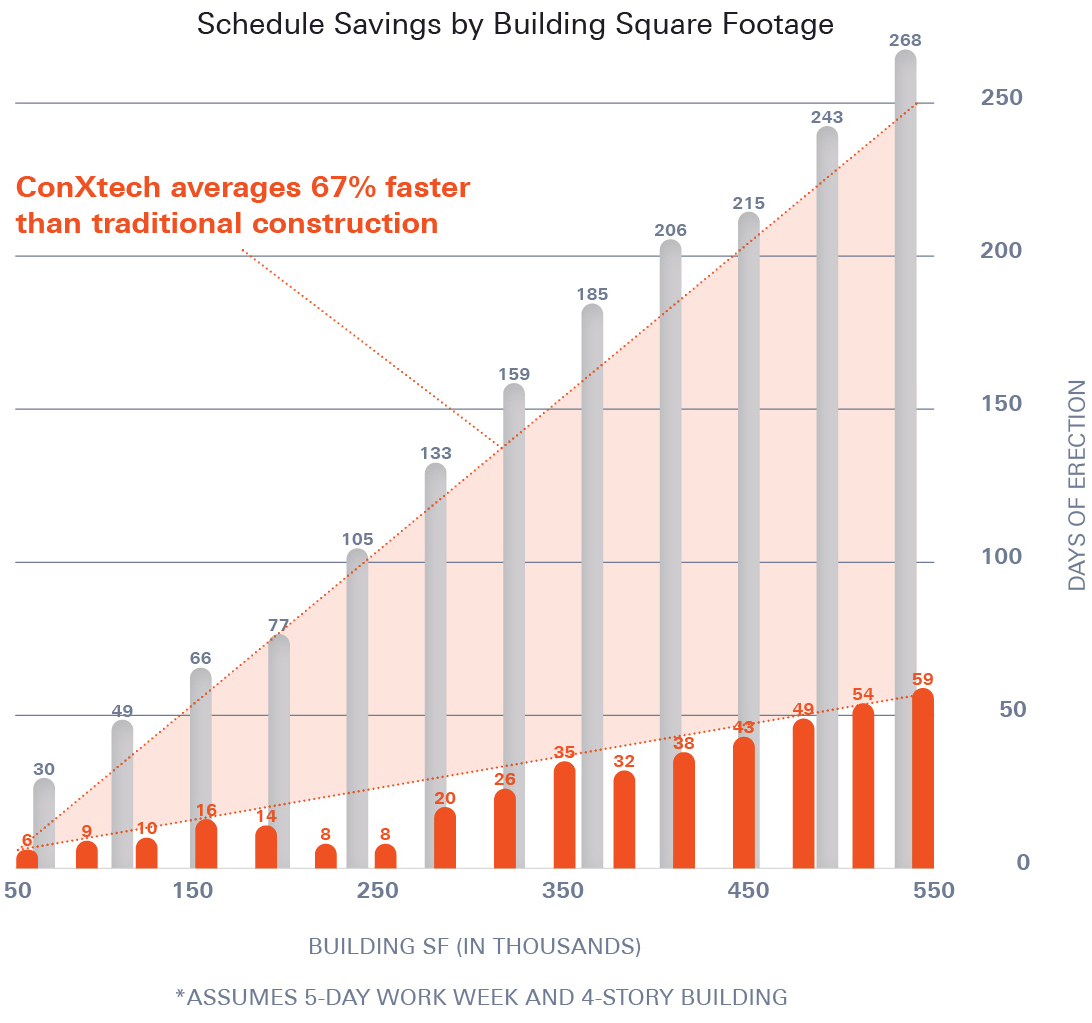
The data indicates that in either case – the higher or the larger the project – the greater the comparative schedule savings versus a traditional steel erection process. The comparative benefit is most prominent, however (by about 30% per story), as the building increases story-to-story, given the unique process advantage of the ConXtech system.
The economic impact of these schedule savings is substantial. On a recently-constructed data center project, one client analyzed the economic impact of using ConXtech.
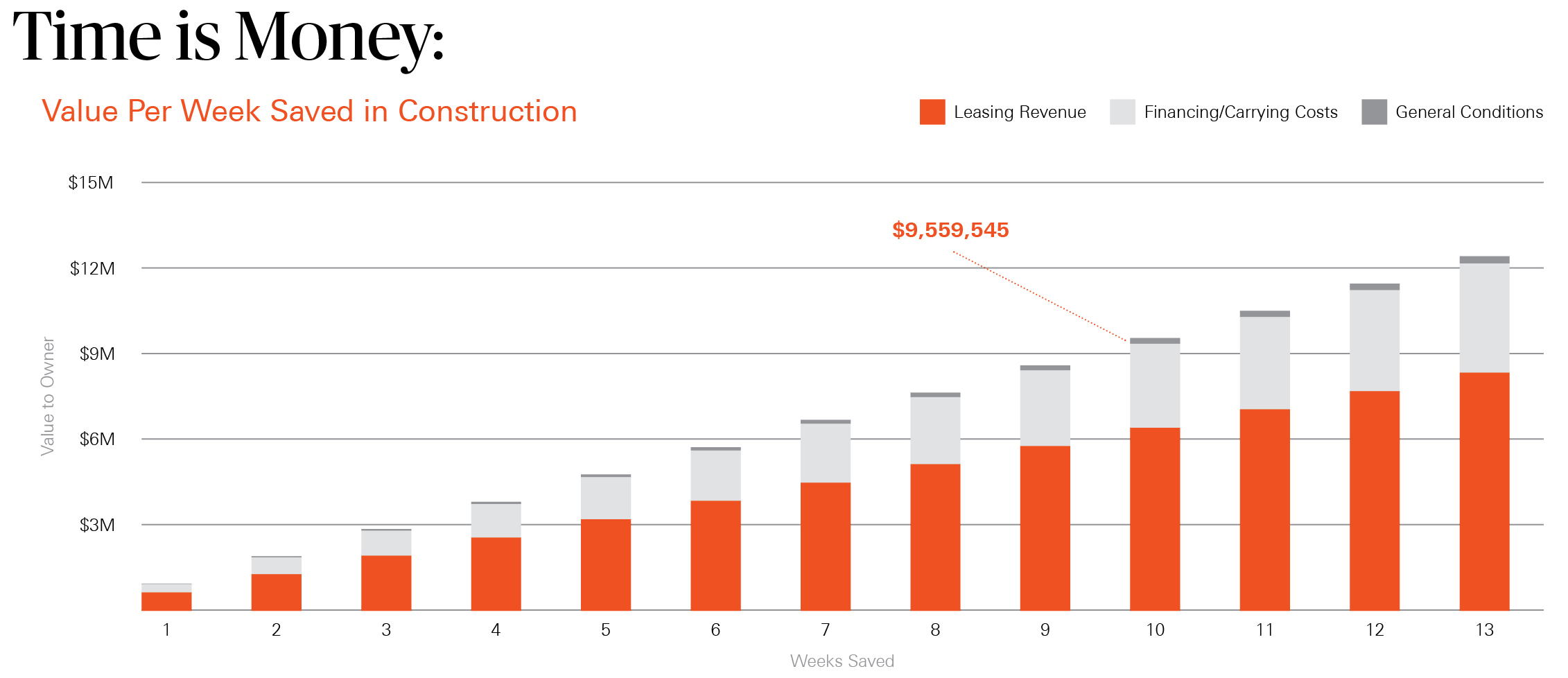
The general contractor suggested that somewhere between 10-12 weeks were saved using the ConXtech system, and the above chart illustrates the value of those weeks in the eyes of the owner (note these numbers have not been escalated to reflect today’s value).
Succinctly,
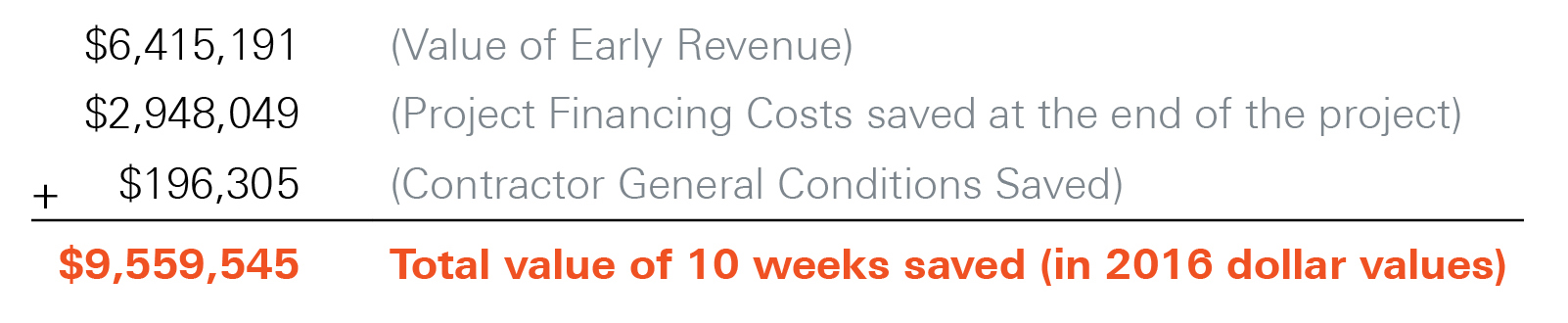
Economic benefits will depend on the dynamics of each project, primarily driven by the scale of the project, financing costs, and projected revenue.
ENGINEERING FOR SPEED
CONCLUSION
Conclusion
Conclusion
Early-procurement solutions like those offered by ConXtech are a powerful tool in an engineer’s design toolkit, offering an unparalleled way to accelerate construction schedules while offering broad design flexibility. ConXtech is a strong solution for buildings from 2 to 8 stories, and the flexibility of the system’s kit of parts offers a wide range of structural configurations suitable for anything from schools, healthcare, apartments, and hotels to data centers, biotech applications, and aerospace facilities.
For the right building projects, a ConXtech structural solution can speed up building framing by 3-5x, and ensures greater accuracy both during both the design phase and the construction phase of a project. The unique “lower and lock” erection method facilitated by ConXtech collars reduce or eliminate on-site welding, and the precision of its components can reduce project risk and provide a meaningful return on investment for developers and building owners.